We use cookies to make your experience better. To comply with the new e-Privacy directive, we need to ask for your consent to set the cookies. Learn more.
Prevention above Cure
Emerio testing program
We do our own quality testing and systematically use the data to improve our products. Emerio products exemplify sustainability and thus improve your reputation. We don’t just rely on certifications. A GS or CE certificate doesn’t tell you everything about safety or EU regulations.
Testing program
Our test program
In our test program we do checks during the entire production process. From the design till its on the market. We believe that prevention is better than damage control afterwards.
We manage our risks by checking for defects or hazardous chemicals before the product enters the market. We work to protect our and your reputation by avoiding recalls and taking care of the environment as well as consumer health. We care about quality.
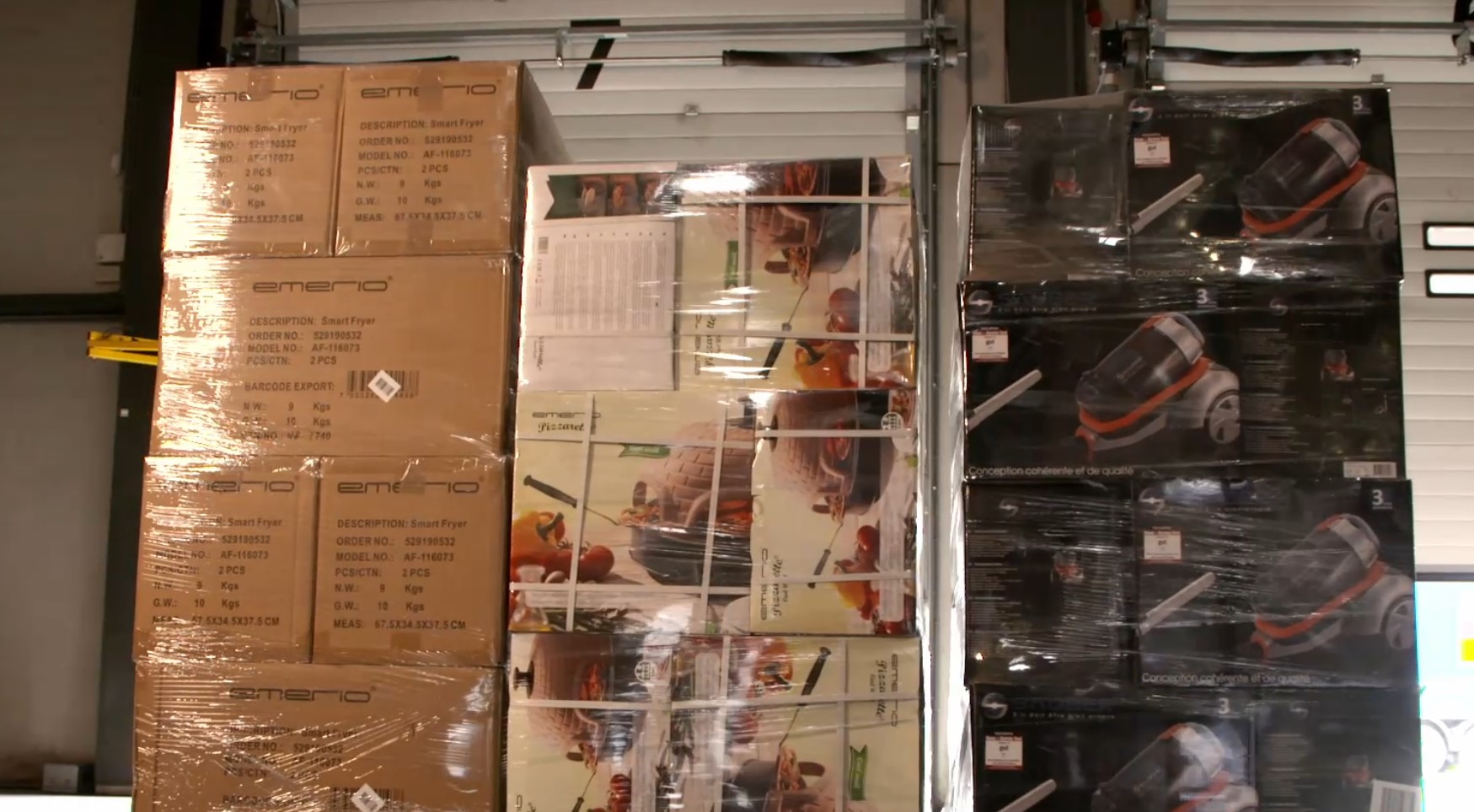
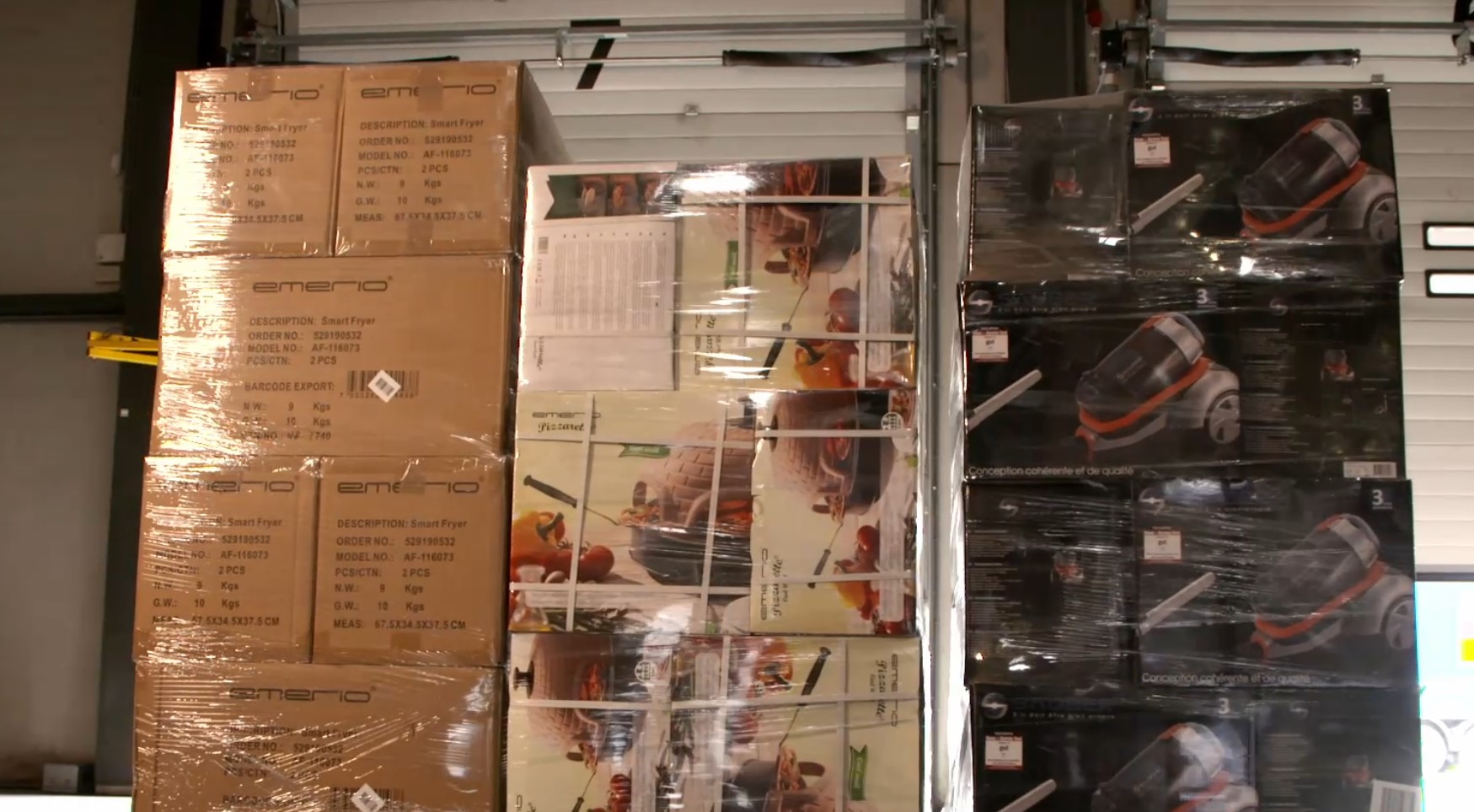
Incorporating teamwork
We have successfully combined our expertise in electrical household appliances with several well known laboratories on safety and testing. This is how keep track on new EU regulations. Together we offer you the most extensive and profound quality control to guarantee the success of our products.
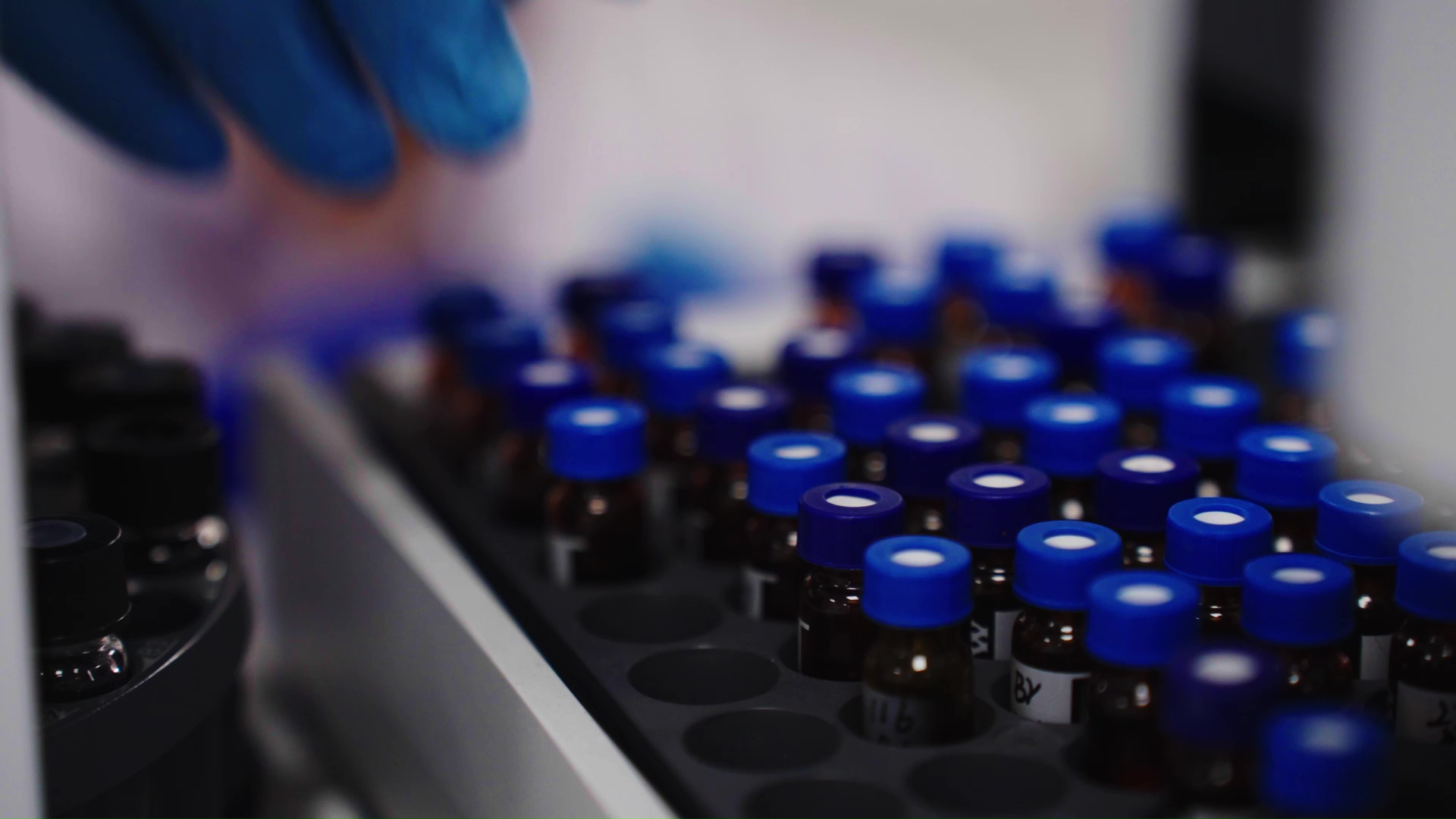
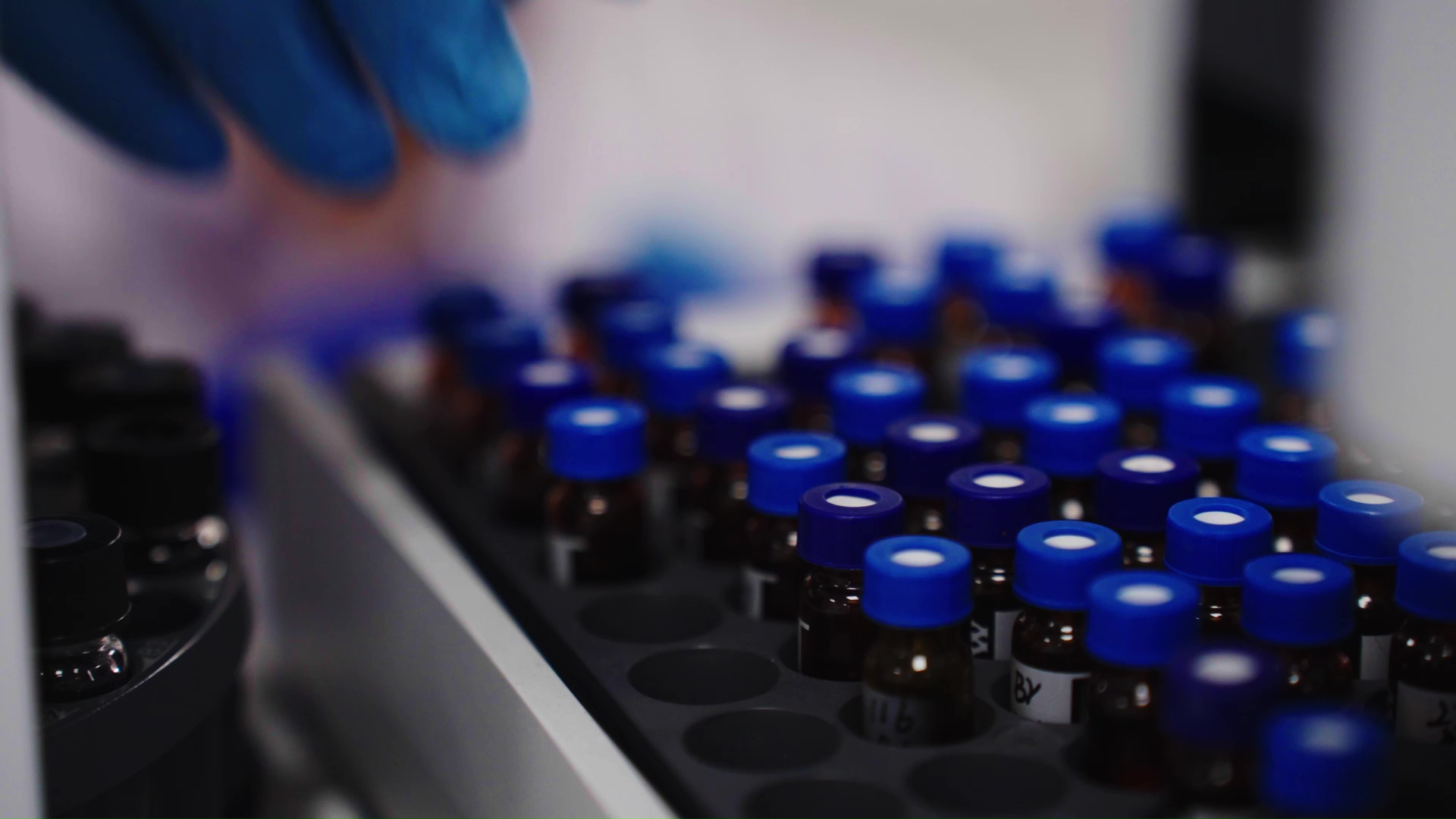
Our Approach
At Emerio we test all of our products extensively at every stage of the production process and we start even before we place an order. Our testing roadmap;
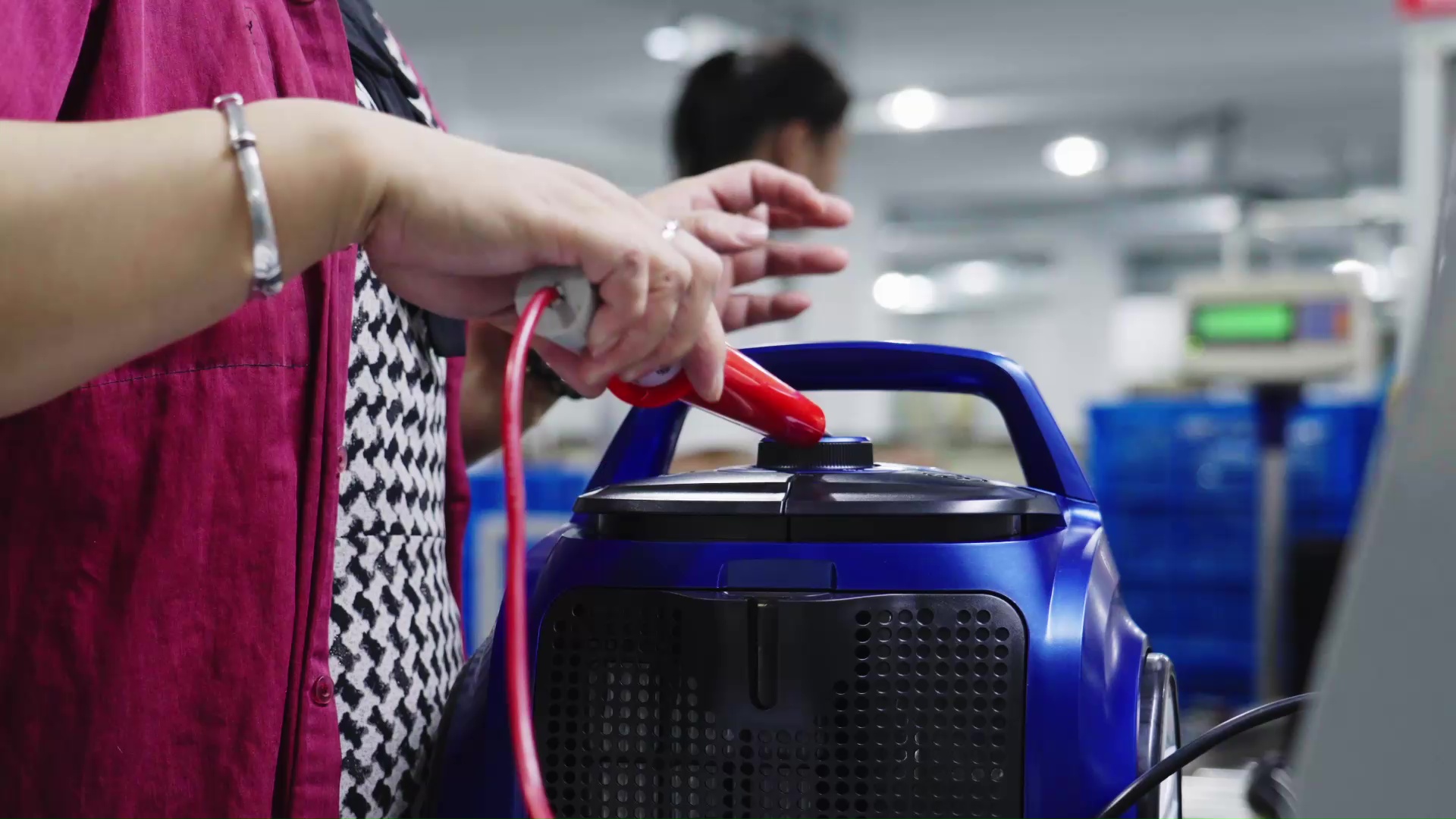
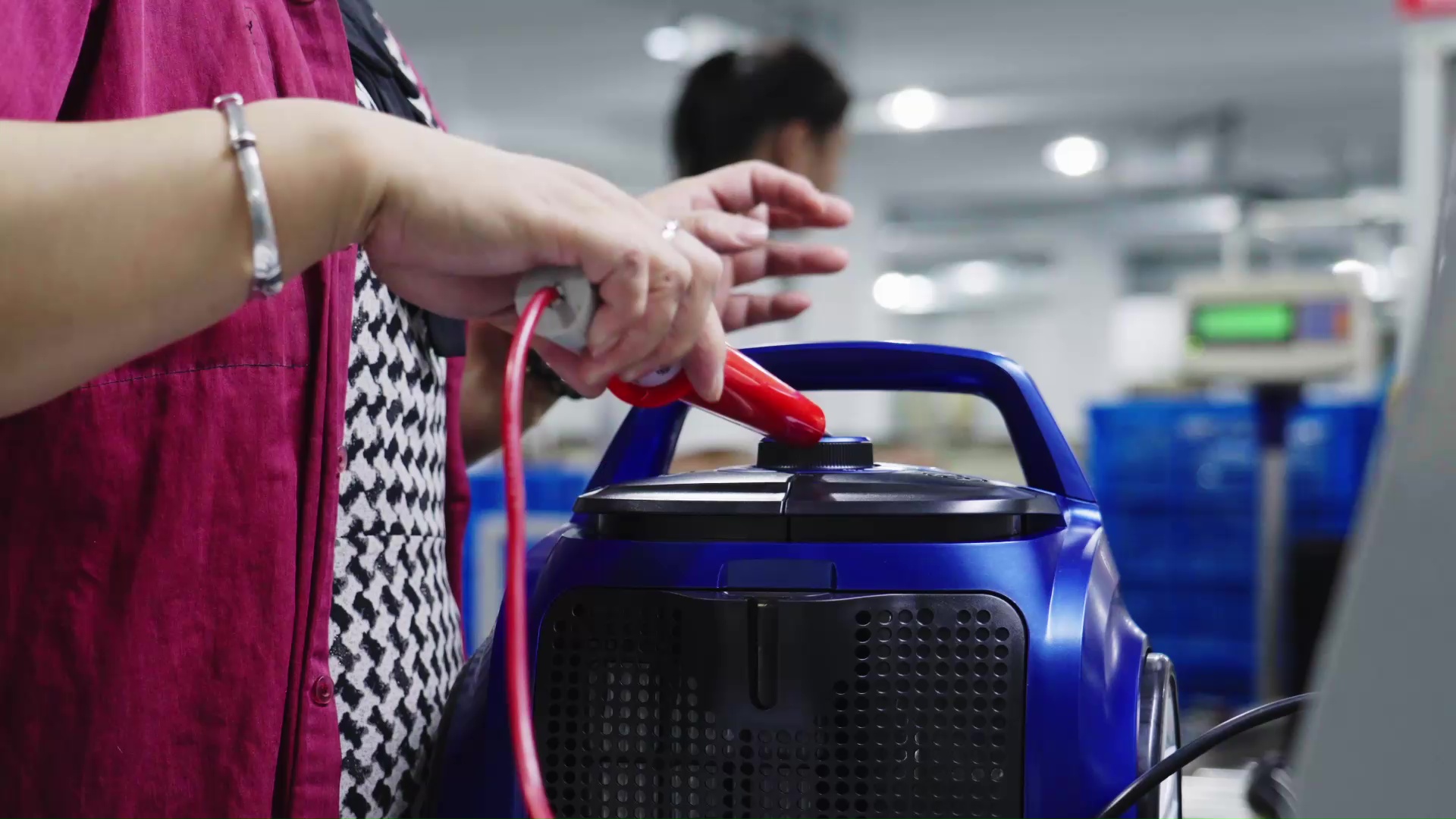
FACTORY AUDIT
Before Placing the Order
FACTORY AUDIT
Before placing an order we make sure that the producing factory has the necessary infrastructure, systems, processes and capabilities to execute it.
Our factory audit contains:
- manufacturing capabilities
- product risk analysis
- quality assurance
- material control system
- cleanliness, health and safety
- environmental compliance
- hazardous chemical management
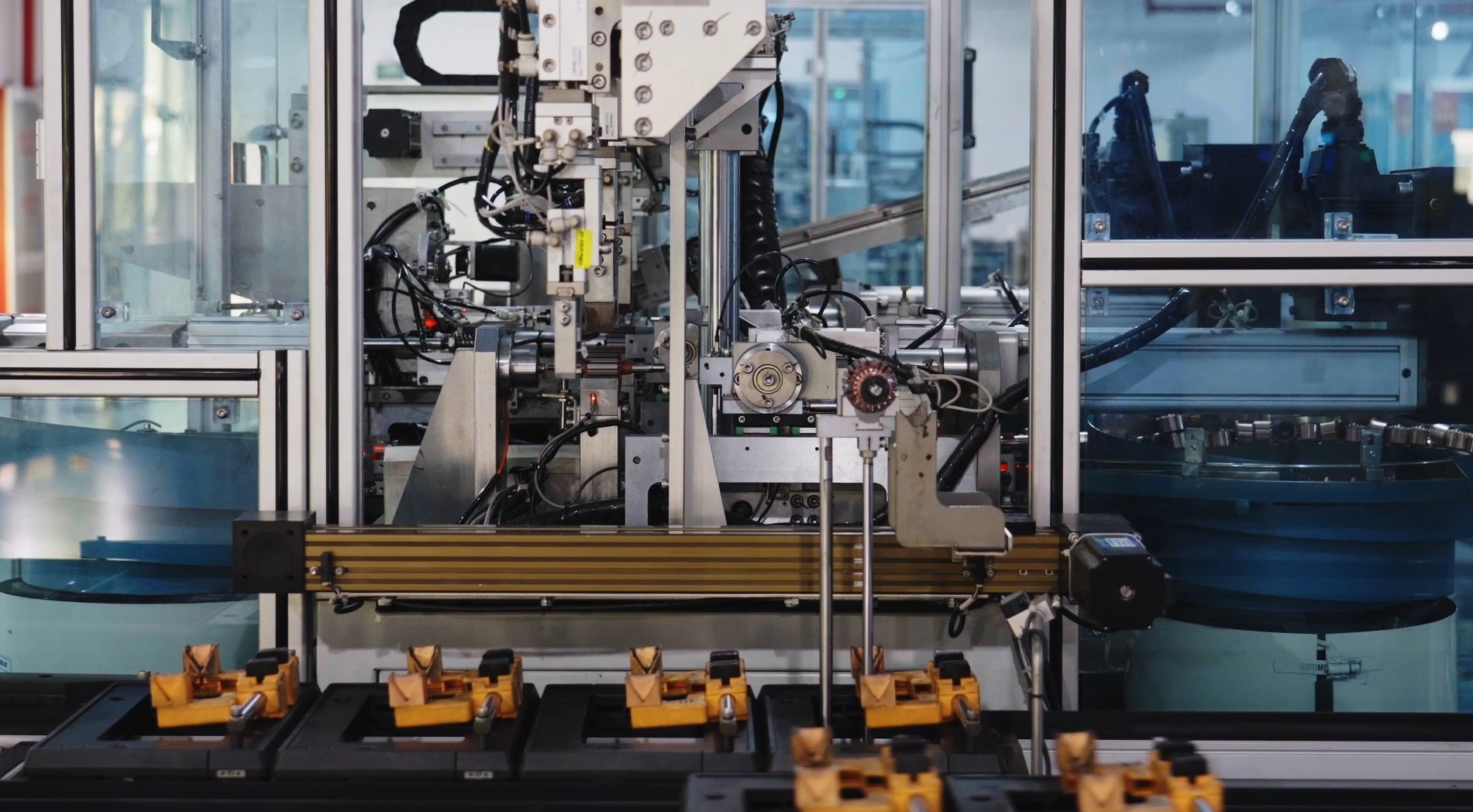
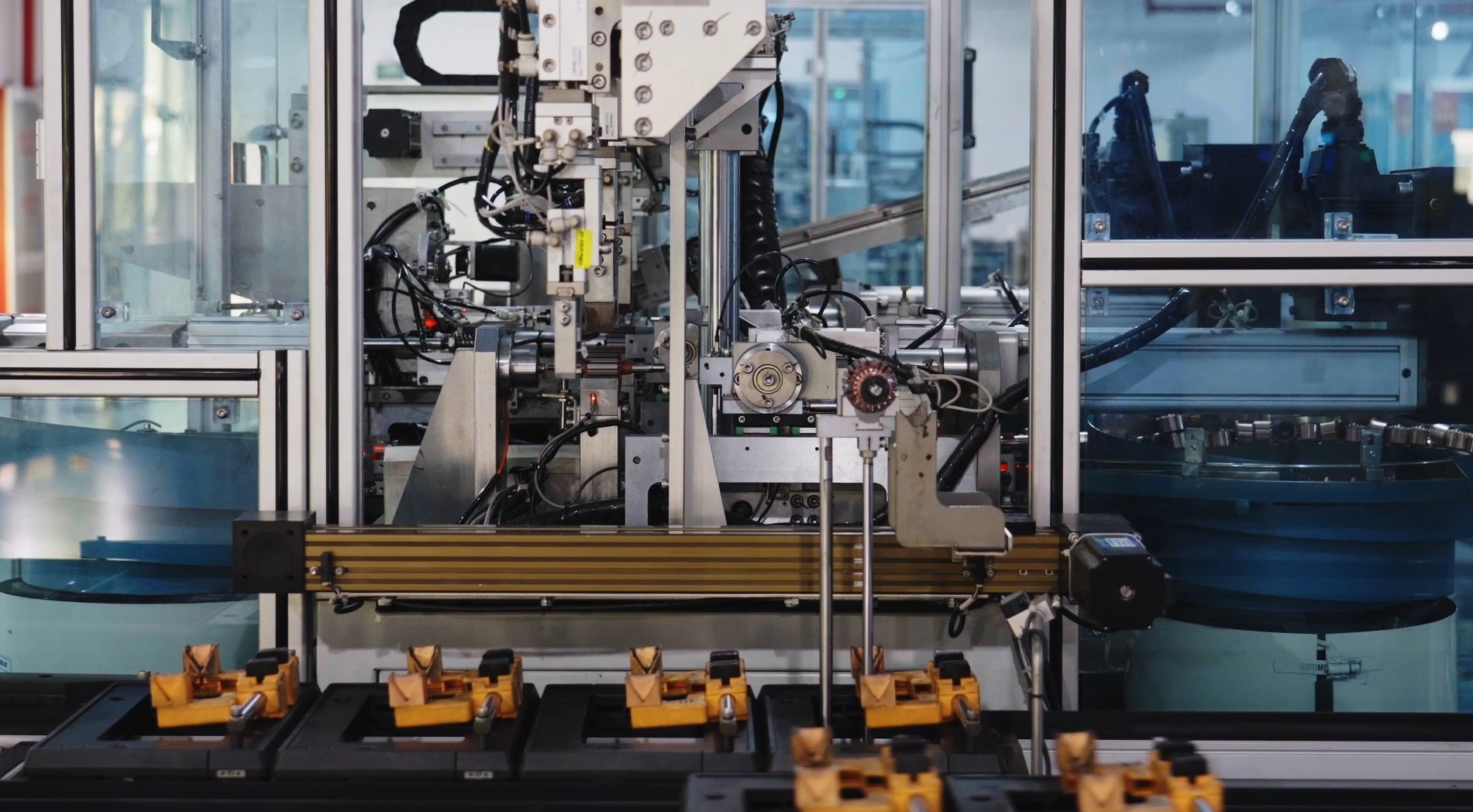
BSCI COMPLIANCE
Before Placing the Order
BSCI COMPLIANCE
We are a BSCI partner and ensure that our suppliers also comply with international standards, respect workers‘ rights and improve working conditions in the factories.
CERTIFICATION
We make sure that all certificates are correct and valid. We document all certificates accurately in our software database in Europe. Certifications prove your credibility in the market, but are only relevant if the products are produced accordingly.
QUALITY CONTROL DATABASE
We use our own software – developed and refined by our own experience over many years –to store and monitor technical documents and QC reports. All our offices have immediate access to important technical documentation.
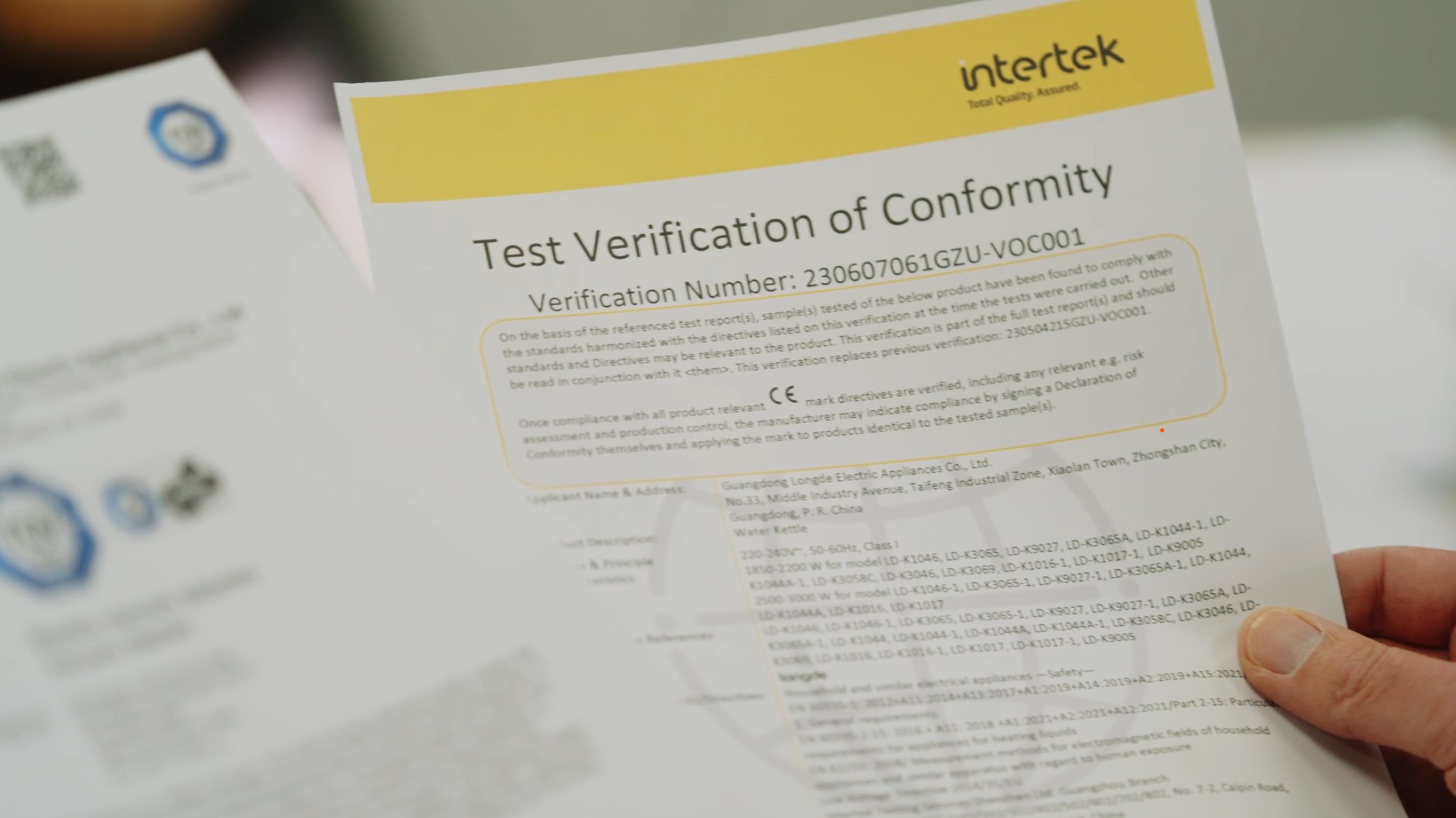
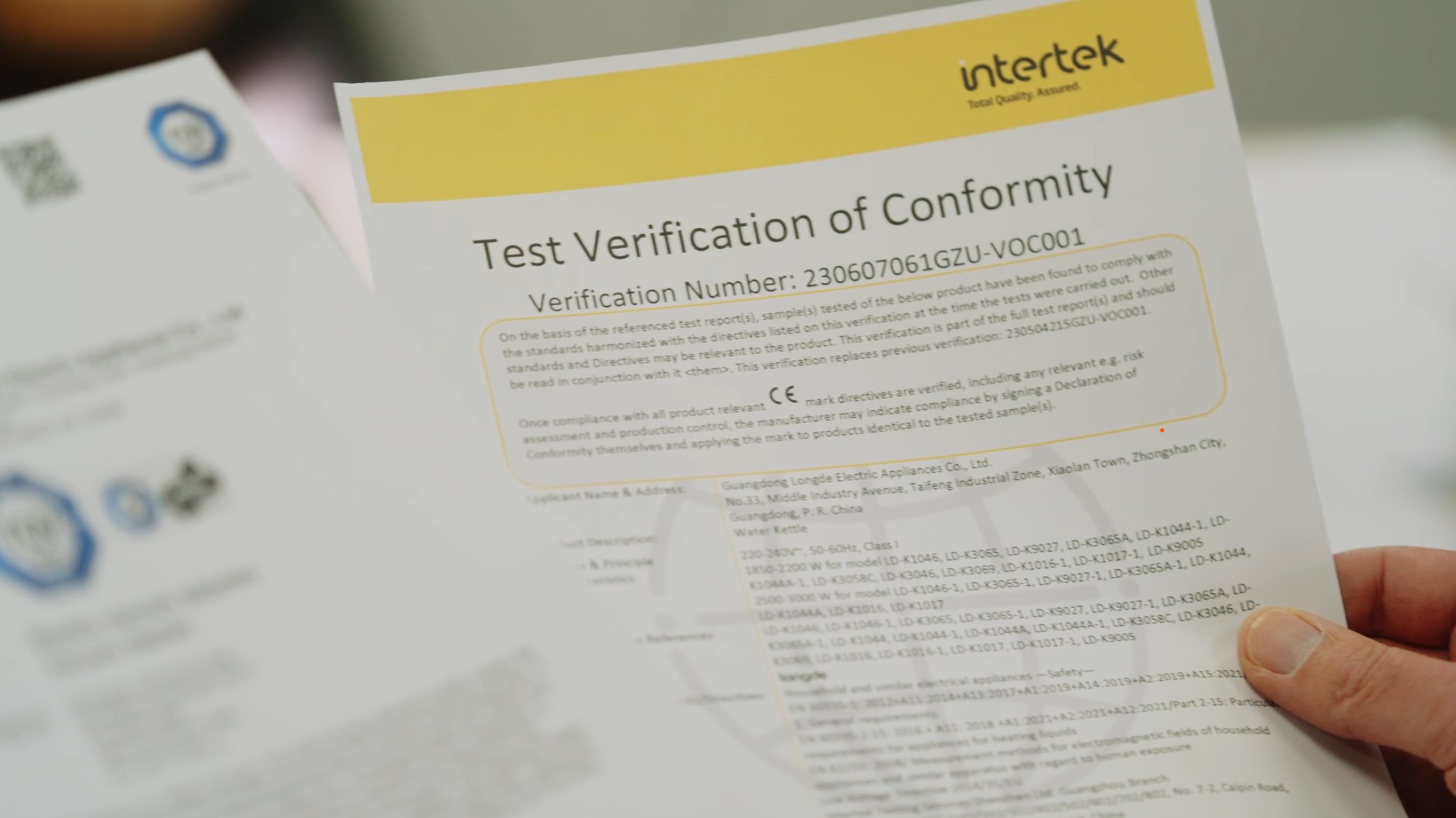
CONSTRUCTION CHECK
Before production
CONSTRUCTION CHECK
Our construction check contains:
- accessibility of live parts
- basic functional usage
- components
- creepage distances
- grounding
- hipot test
- instruction manual
- internal wiring
- rating label
- terminal connections
- sharp edges
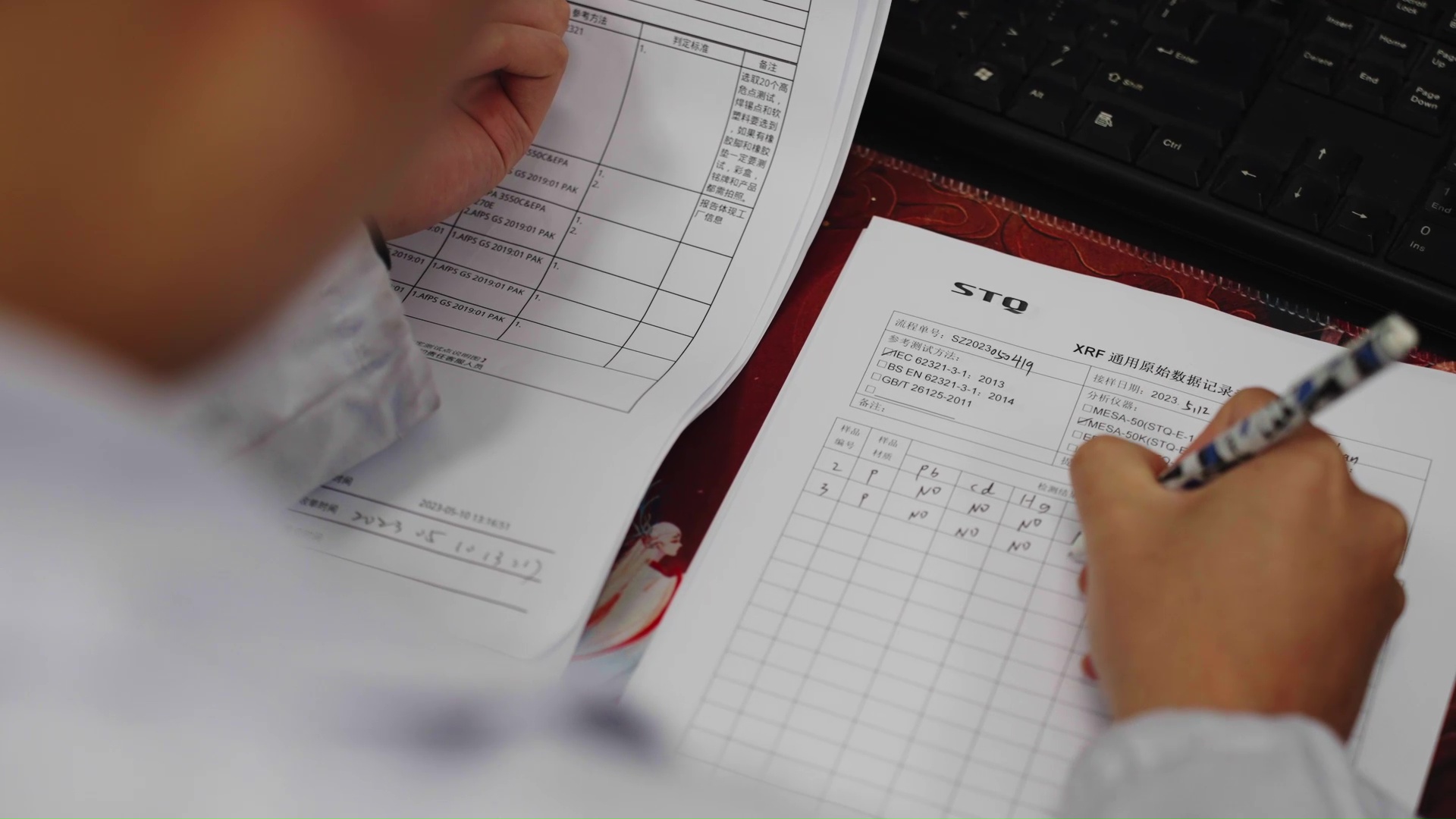
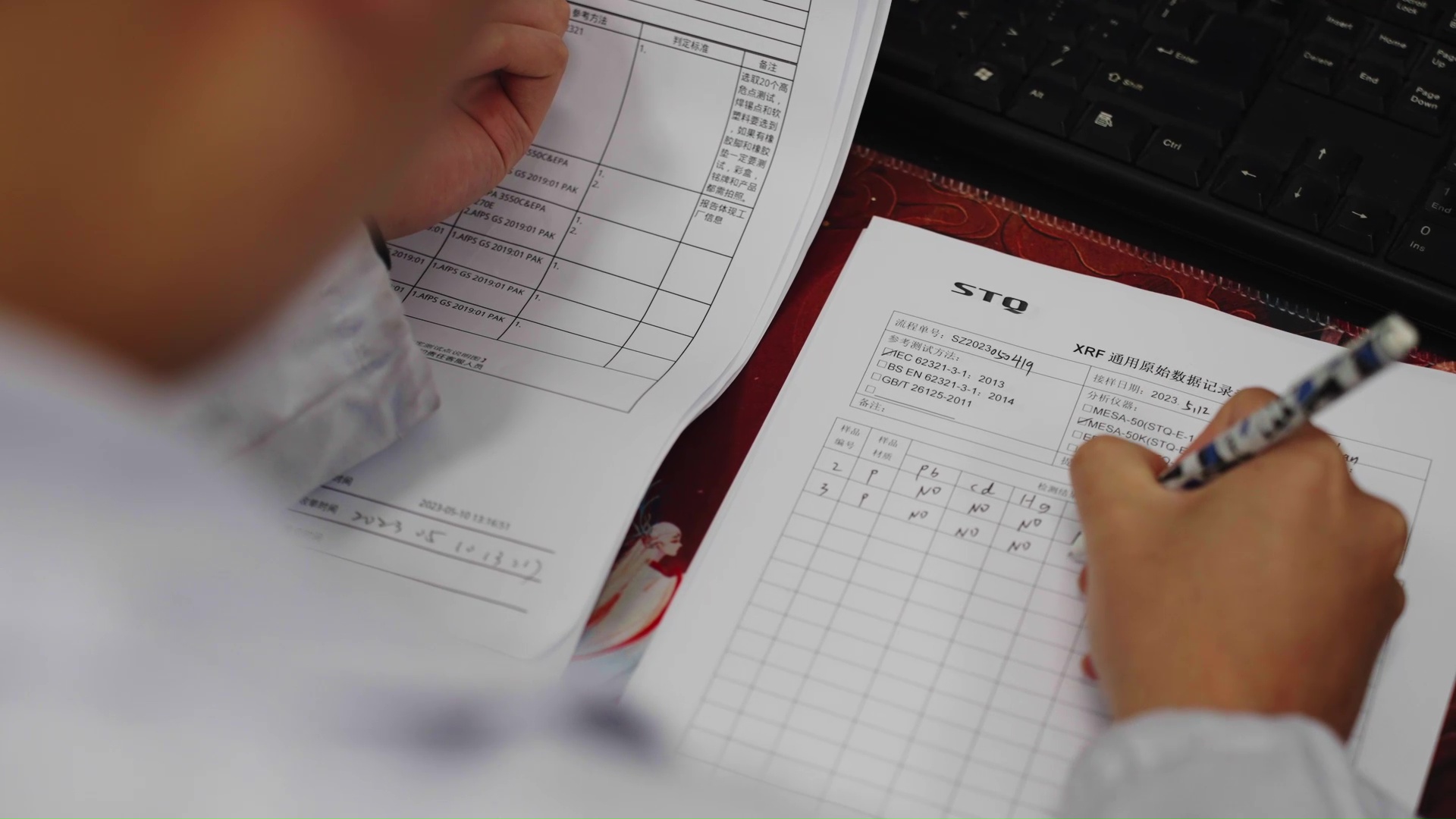
ABNORMAL USAGE TEST
Before production
ABNORMAL USAGE TEST
We test any kind of potential abnormal use of the product by the consumer.
This check is based on:
- product history
- product group
- Rapex history
- QC management
- Test laboratories experiences
Examples:
- What will happen if the consumer fills the kettle with too much water?
- What will happen if you reduce the speed and airflow on a fan heater?
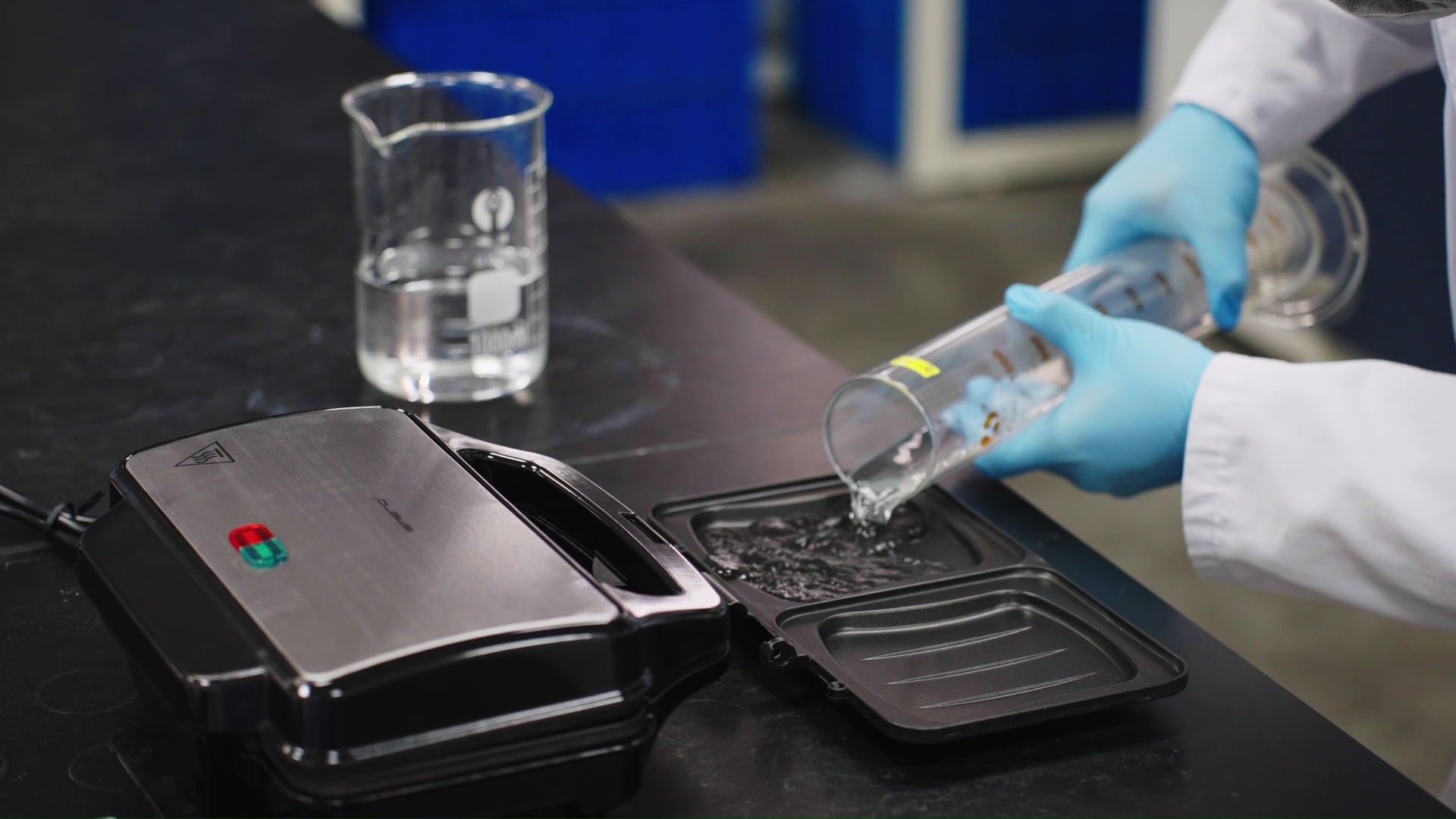
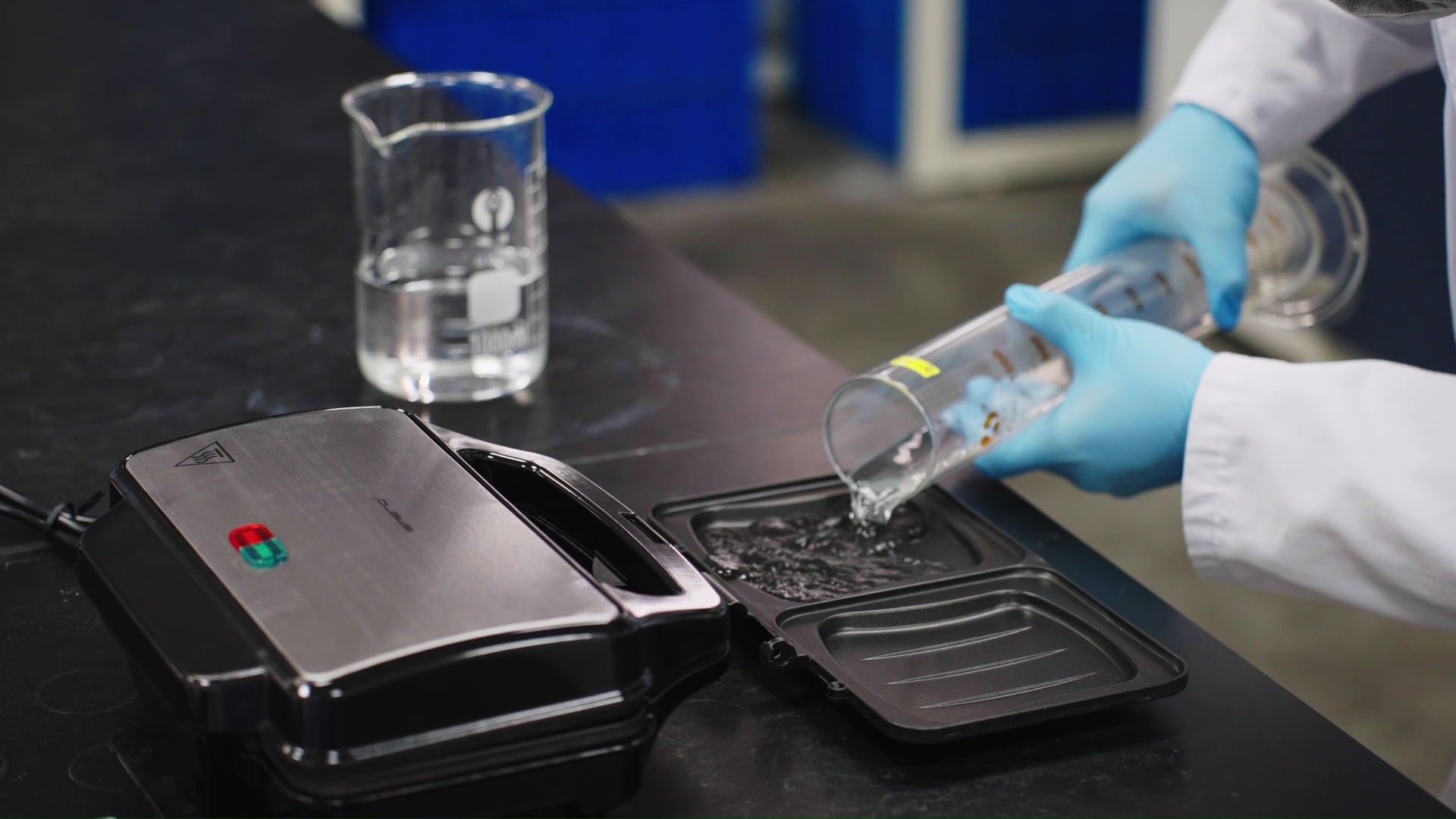
QC PLAN
Before production
QC PLAN
Our QC managers accurately plan what additional tests are necessary for each individual order. This plan is coordinated with our merchandisers, who monitor the orders until delivery.
Our QC managers' decisions are based on:
- product history
- product group
- Rapex history
- QC management
- Test laboratories experience
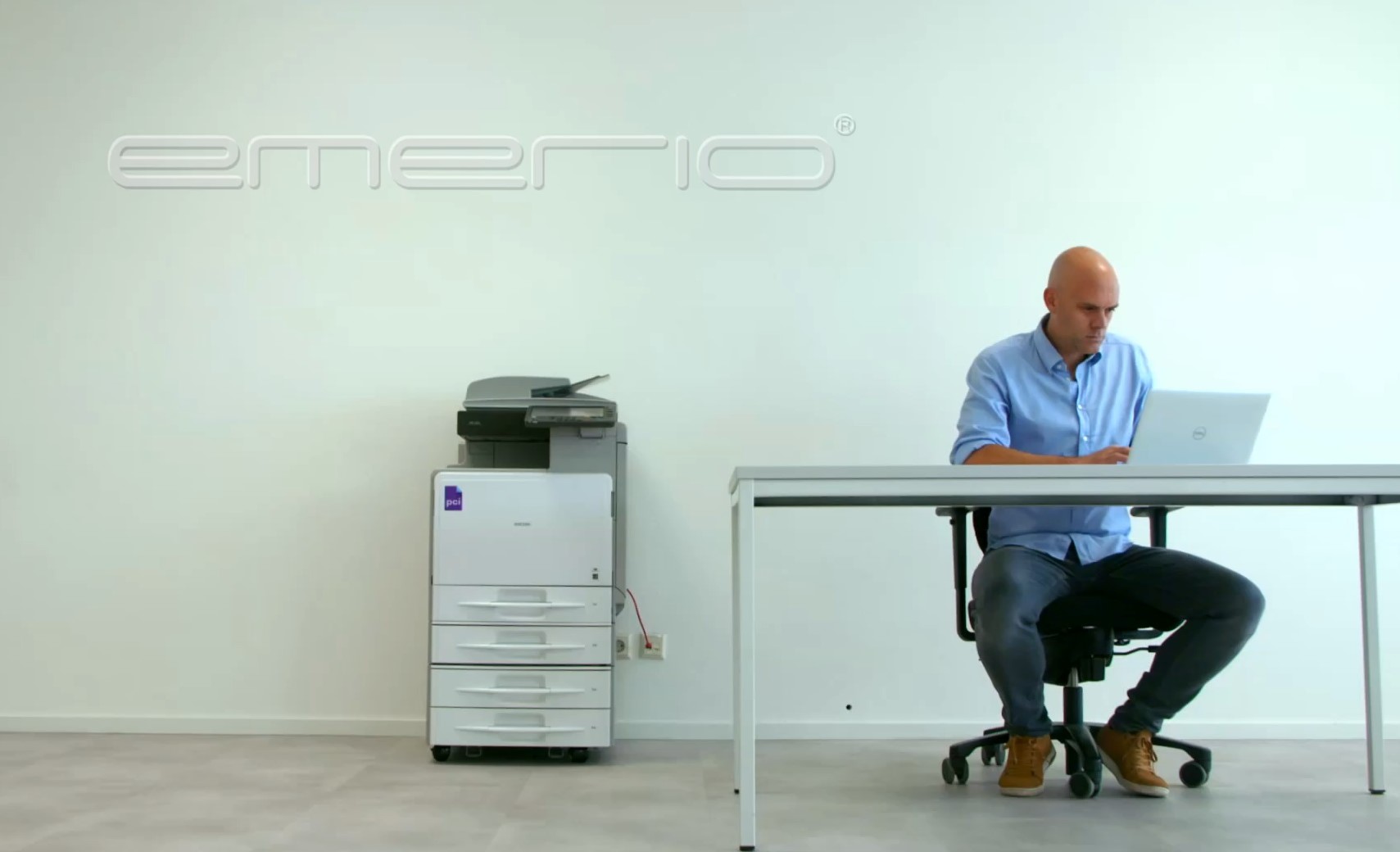
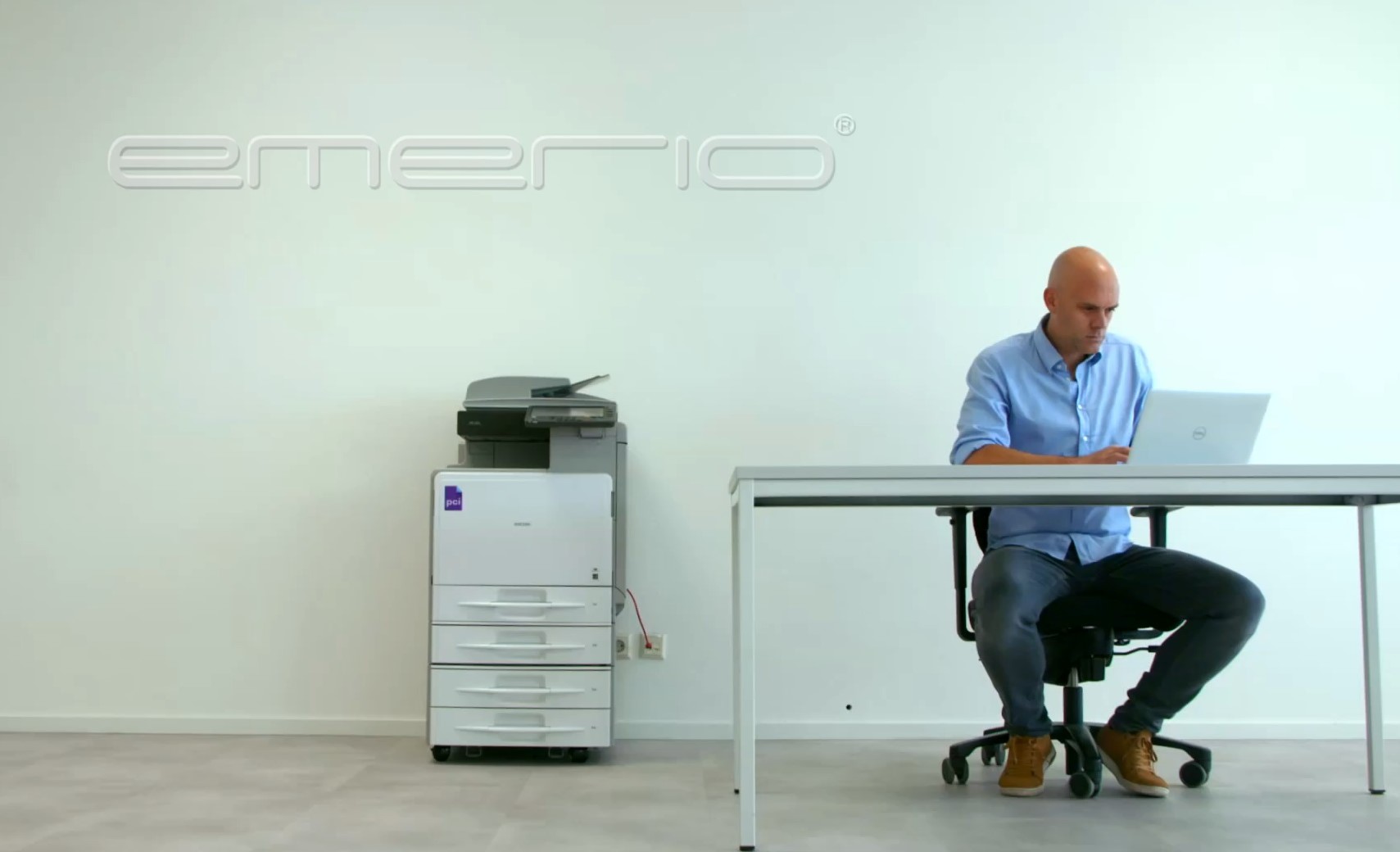
OUR QUALITY CONTROL DATABASE
Before production
OUR QUALITY CONTROL DATABASE
Movies and pictures can be added to our database to help our QC staff prove problems.
To avoid problems occurring repeatedly, we store the history of complaints about a particular item or product group in our database.
We scan each Rapex report for household appliances weekly. We analyse them together with test laboratories to investigate the recalls of similar products from other producers. Thus, we ensure that these mistakes will not happen to our products.
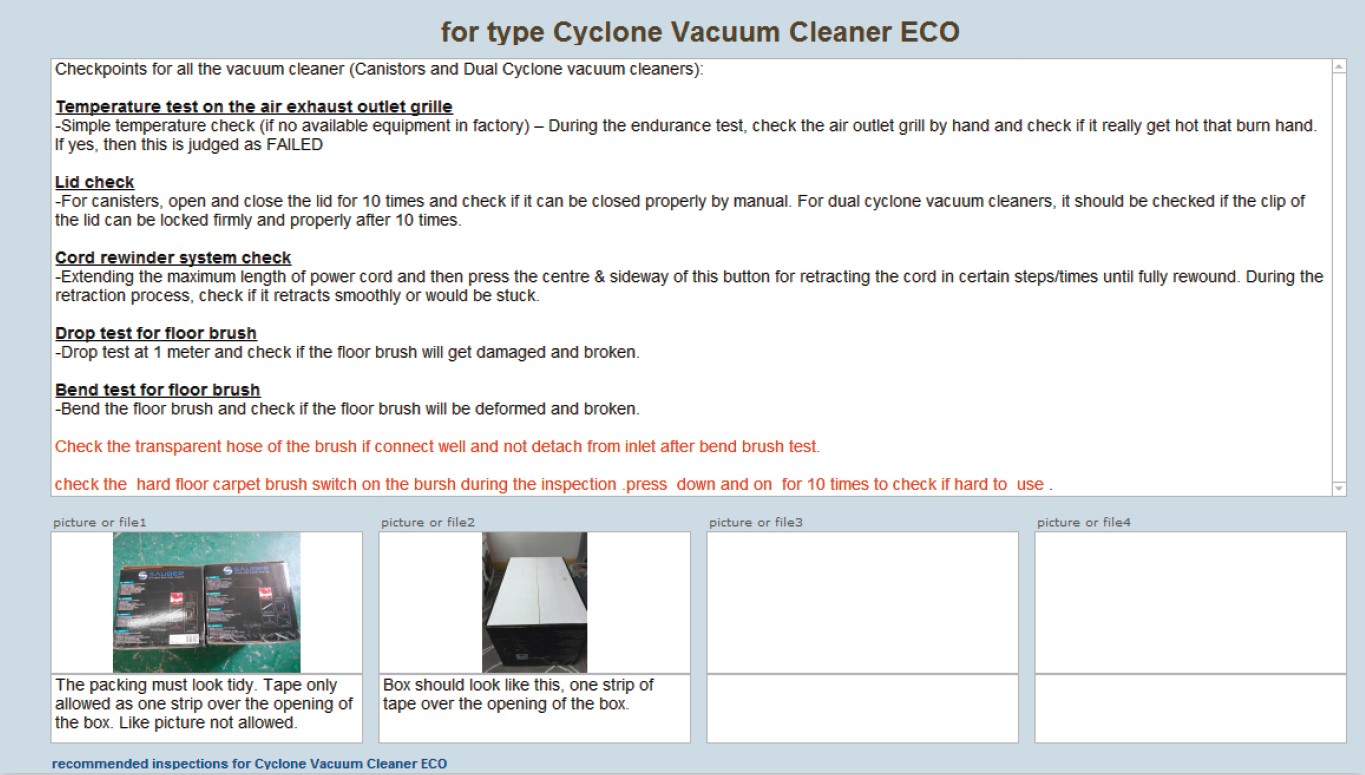
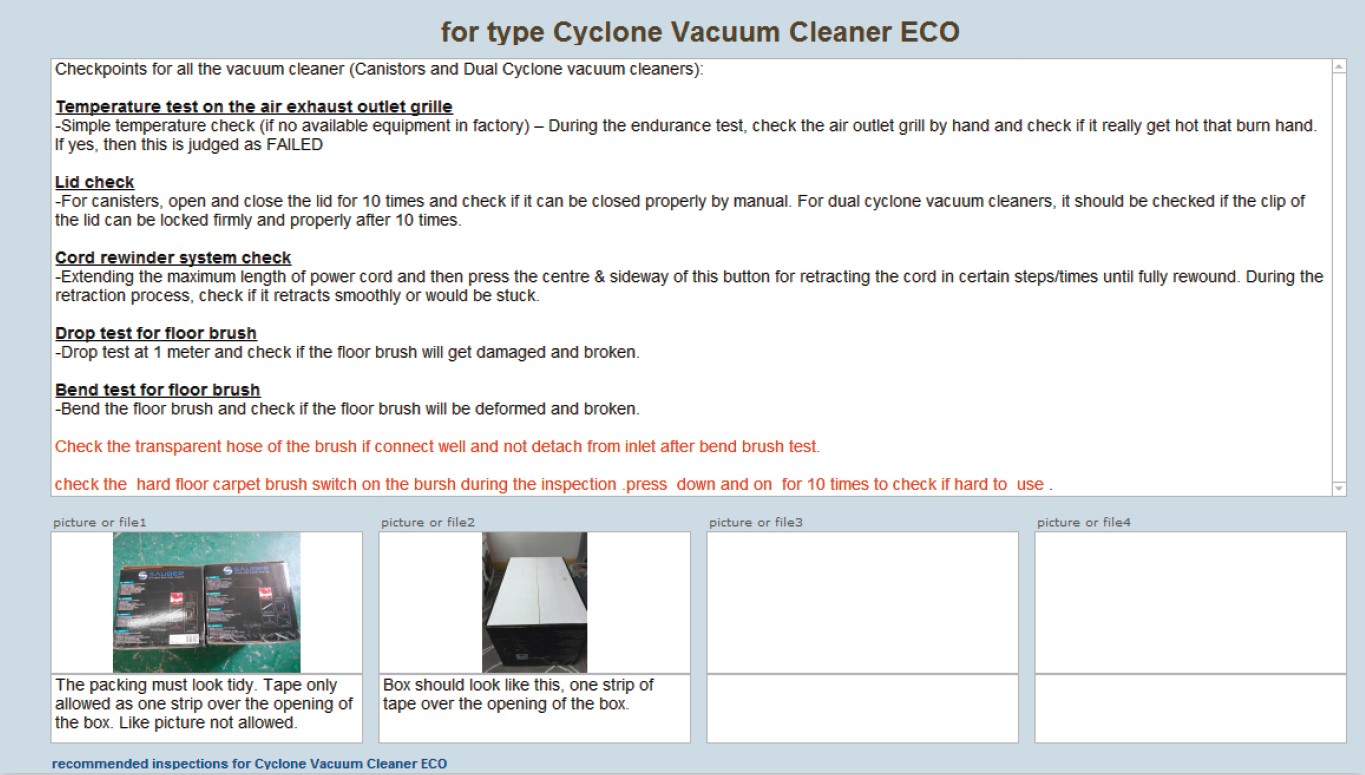
ONLINE INSPECTIONS
During production
ONLINE INSPECTIONS
We carry out online inspections when 10–15% of the production is completed. We inspect the production batch and examine the products in the line for possible defects. At this point we identify deviations and offer advice that will ensure the uniformity and the quality of the product. We also recheck for any defects discovered during preproduction inspection and confirm that they
have been rectified.
We survey a minimum of twenty samples or more if available. The tests are performed according to ISO 2859-1, Level 2 and Level 3. We use our database
to recognize previous problems and to focus on knowledge we have gained from the past.
The inspection also includes:
- abnormal usage test
- additional tests
- designated component control
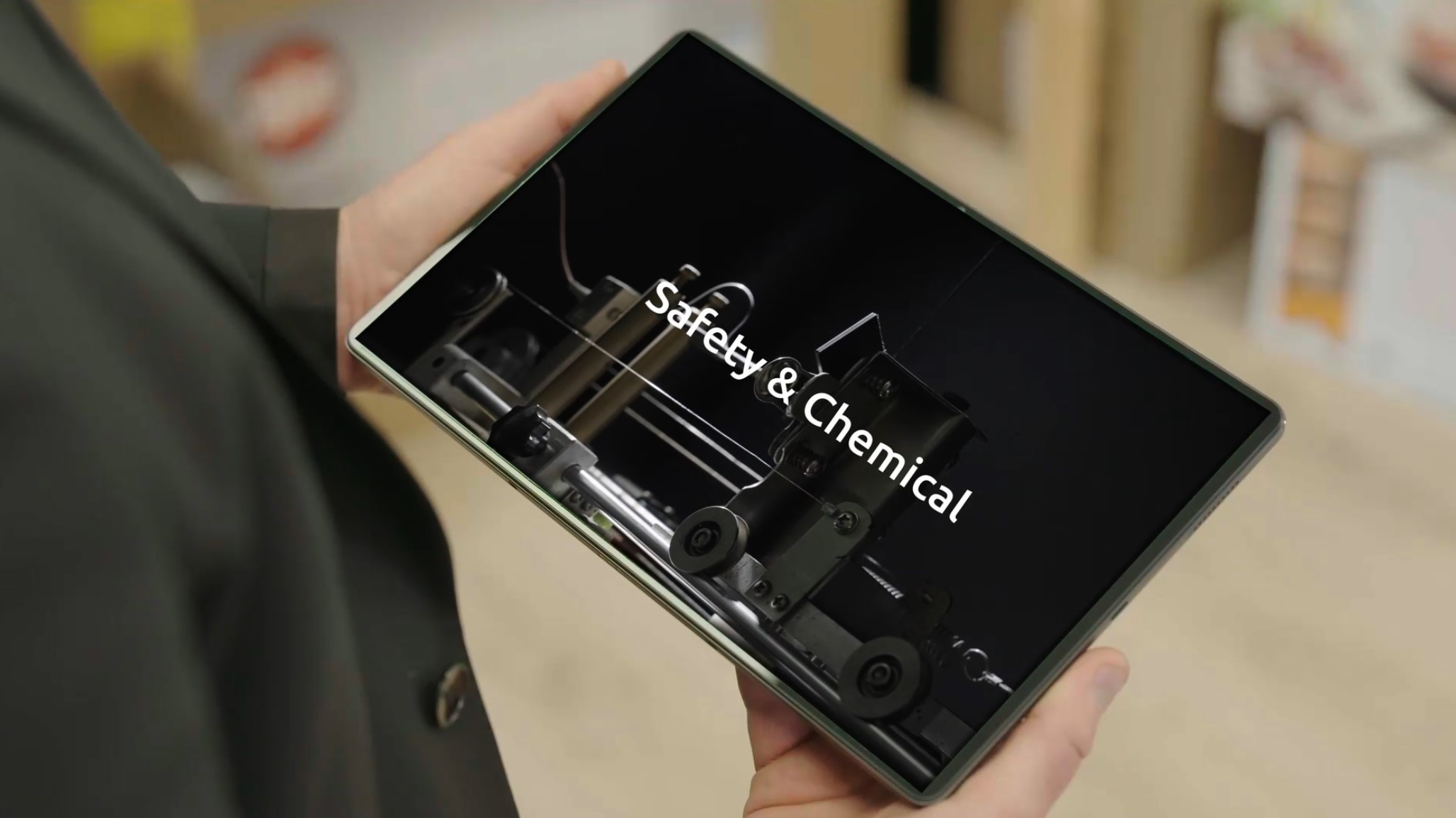
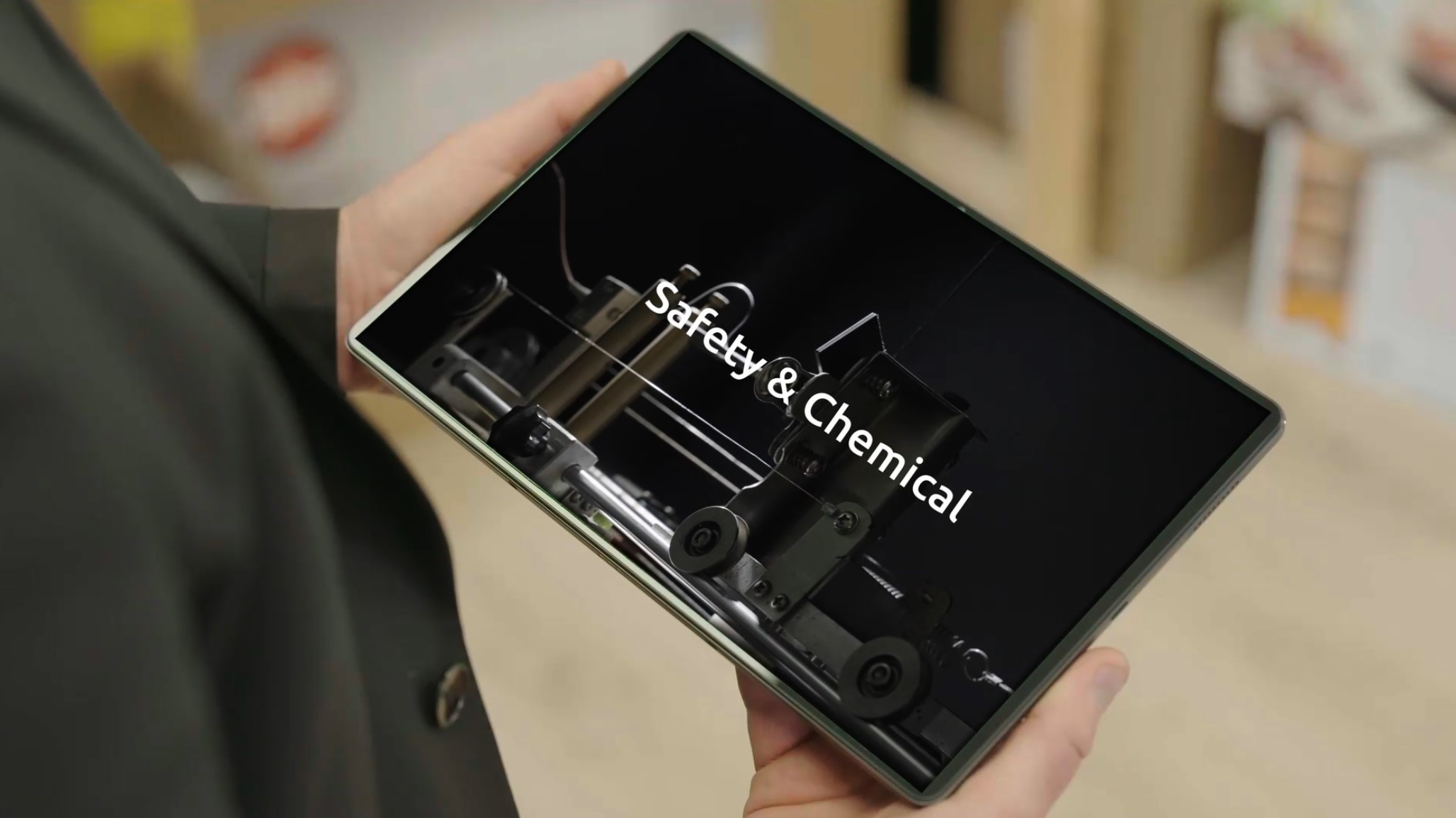
FINAL RANDOM INSPECTIONS
After production
FINAL RANDOM INSPECTIONS
These inspections are to begin after production has been completed and all merchandise is ready and packed for shipment. Our FRI inspection is
performed according to FRI standard Level 2 and 3 to verify product safety, quantity, workmanship, function, colour, size, packaging, and more.
Together with the test laboratories we check the QC history in our own database to ensure previous problems no longer occur.
Our FRI inspection is performed according to ISO 2859-1, Level 2 and Level 3:
- abnormal usage test
- additional tests
- designated component control
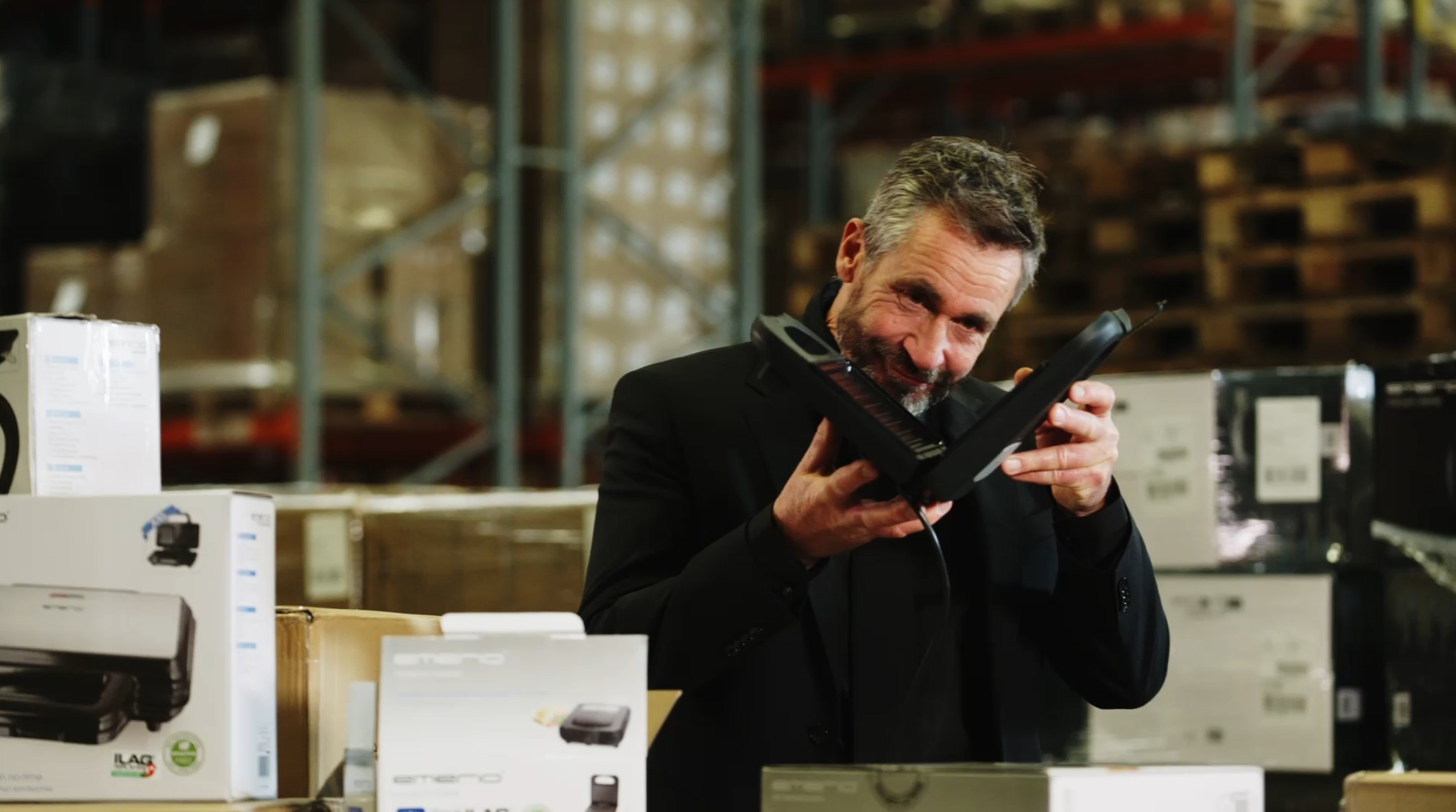
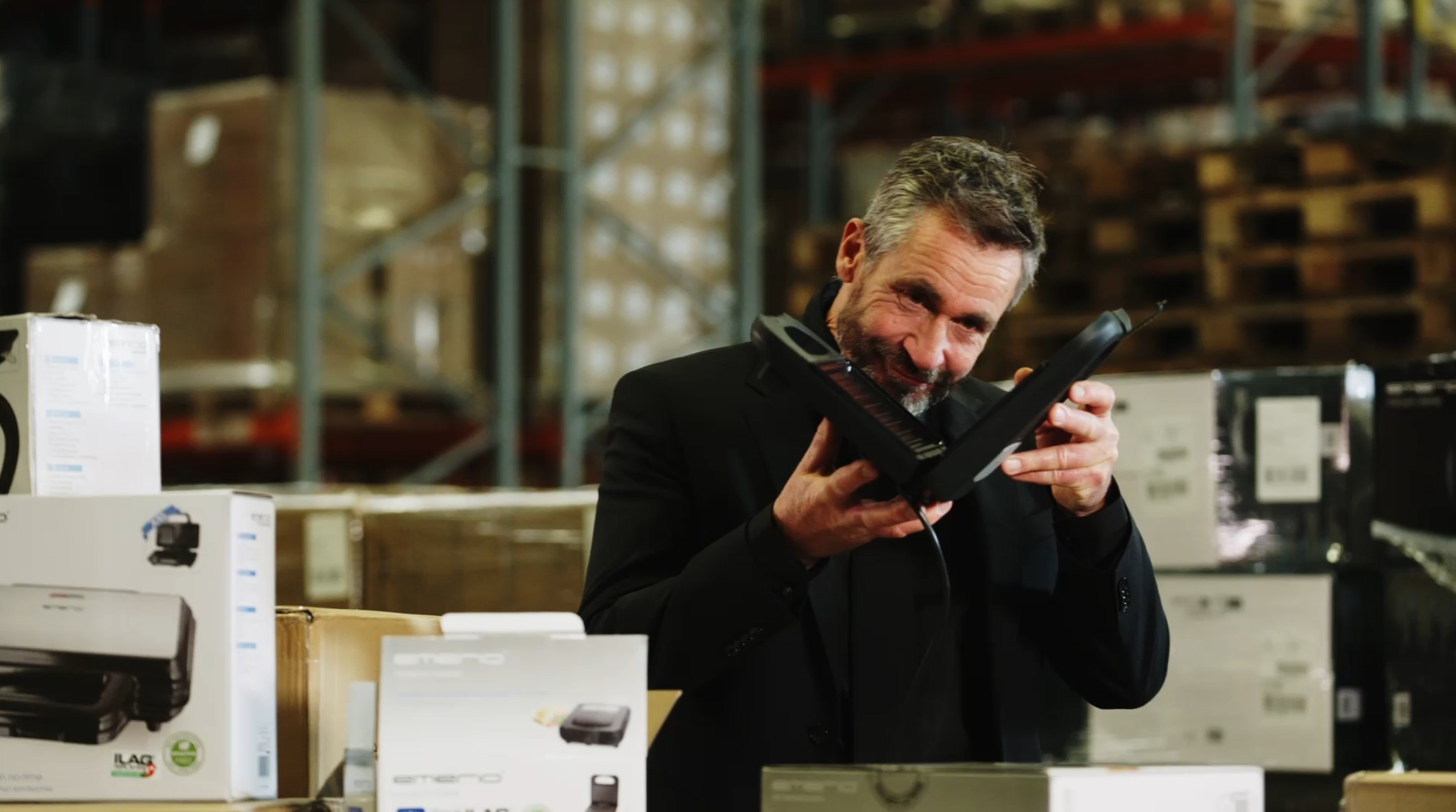
INSPECTION OF RETURNS
After sales
INSPECTION OF RETURNS
Our rating labels state a number for each order that enables us to pinpoint the production date, inspection date and inspection reports. This way we are able to integrate the knowledge acquired from the defects into our quality control cycle to improve future products.
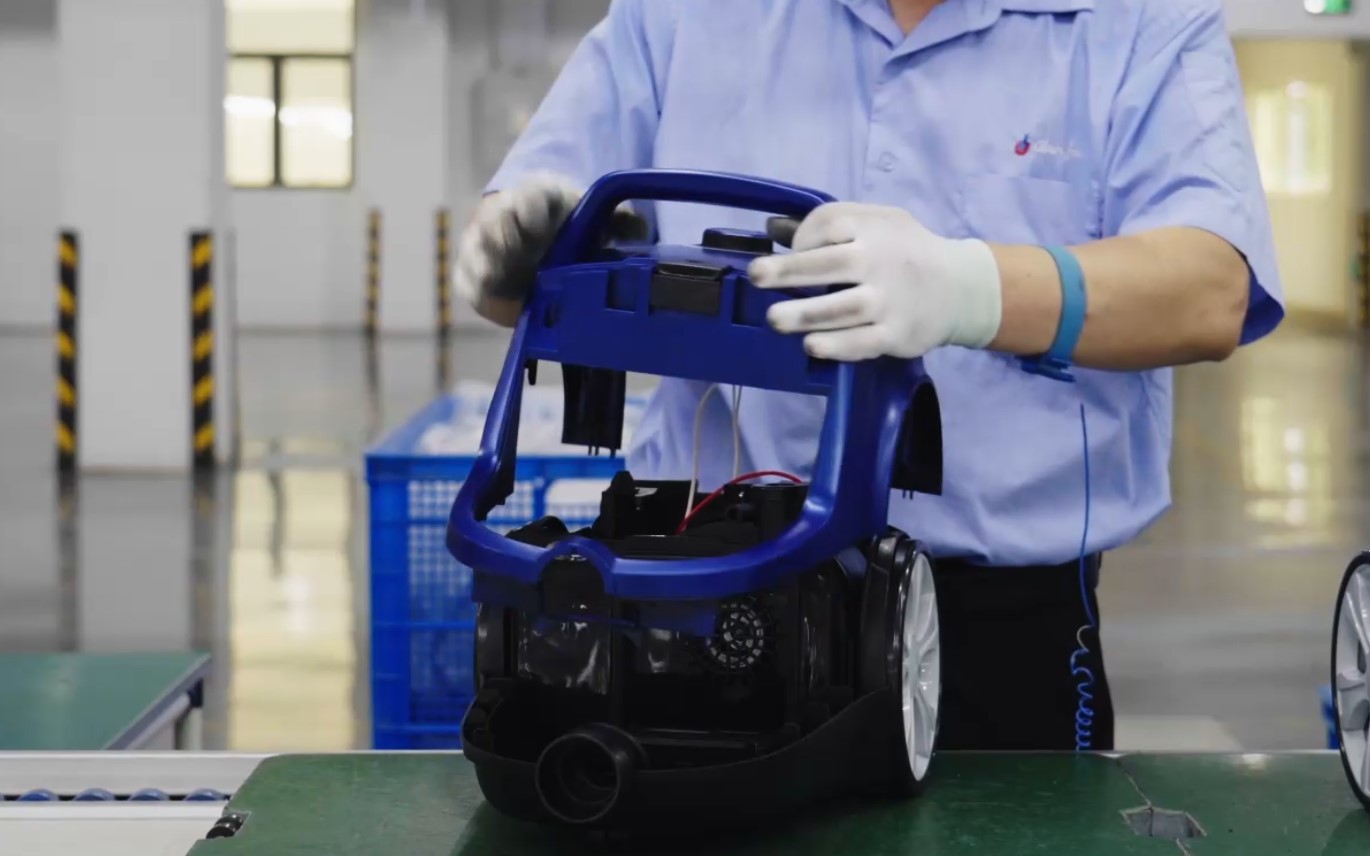
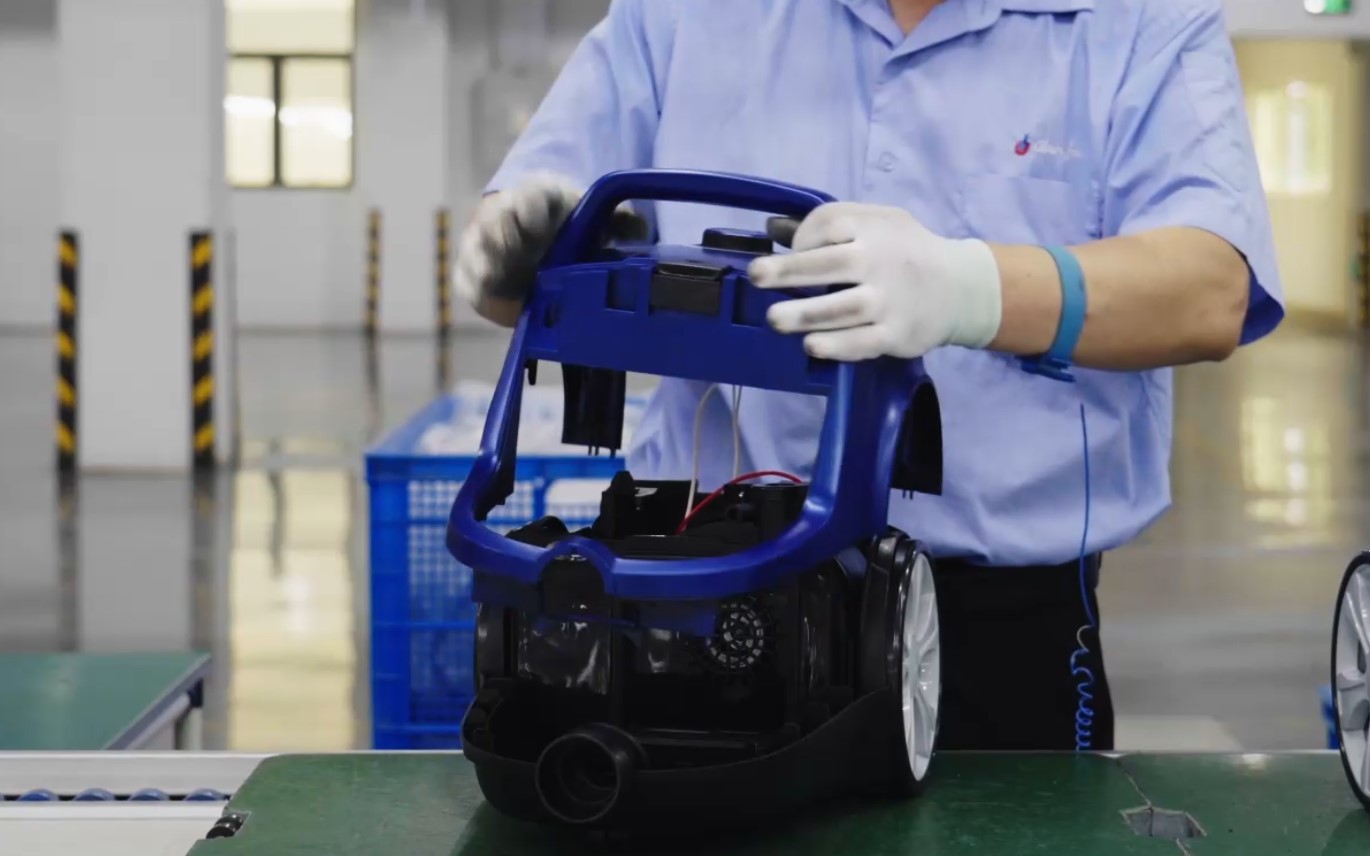
We do our own quality testing and systematically use the data to improve our products. Emerio products exemplify sustainability and thus improve your reputation. We don’t just rely on certifications. A GS or CE certificate doesn’t tell you everything about safety or EU regulations.
Testing program
Our test program
In our test program we do checks during the entire production process. From the design till its on the market. We believe that prevention is better than damage control afterwards.
We manage our risks by checking for defects or hazardous chemicals before the product enters the market. We work to protect our and your reputation by avoiding recalls and taking care of the environment as well as consumer health. We care about quality.
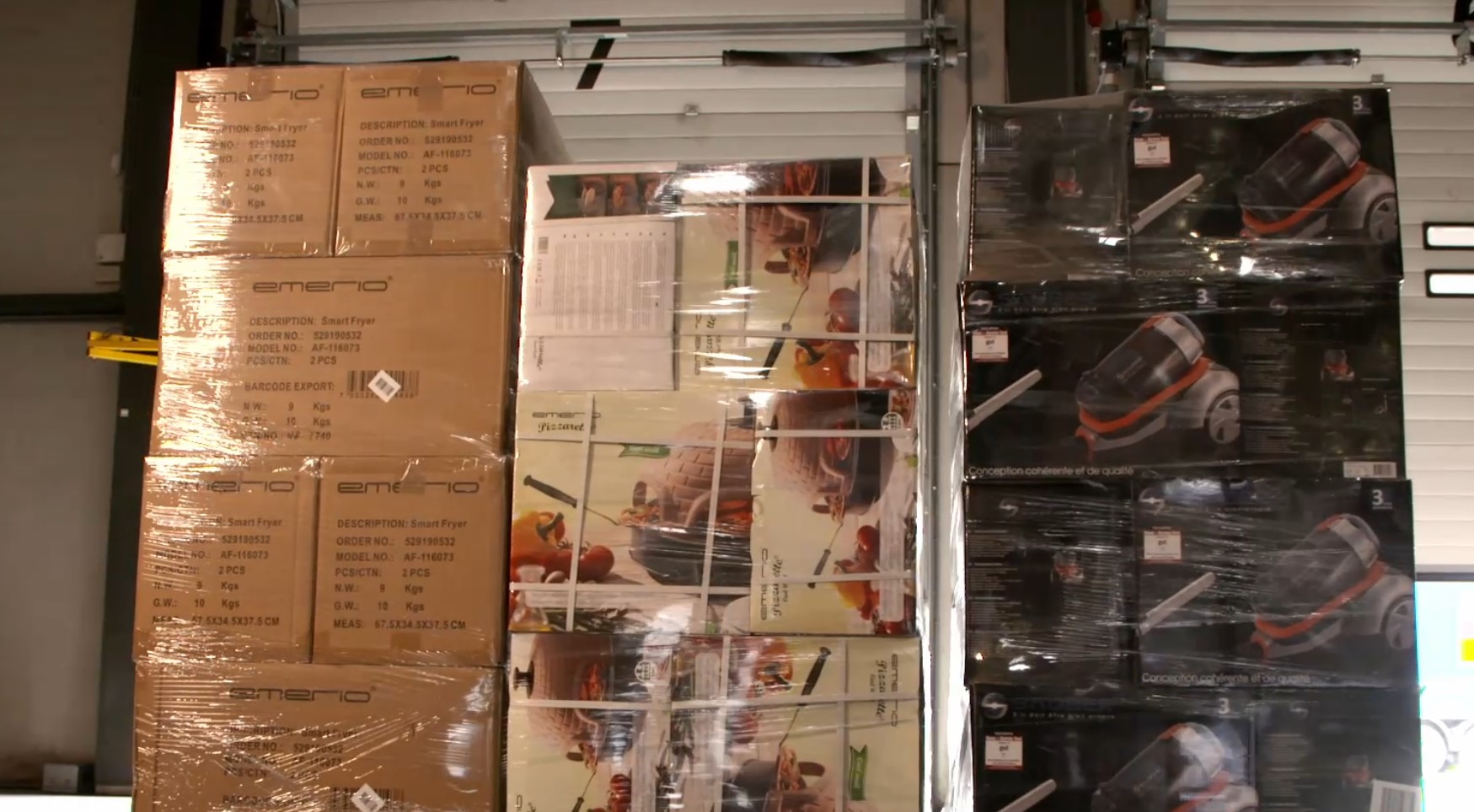
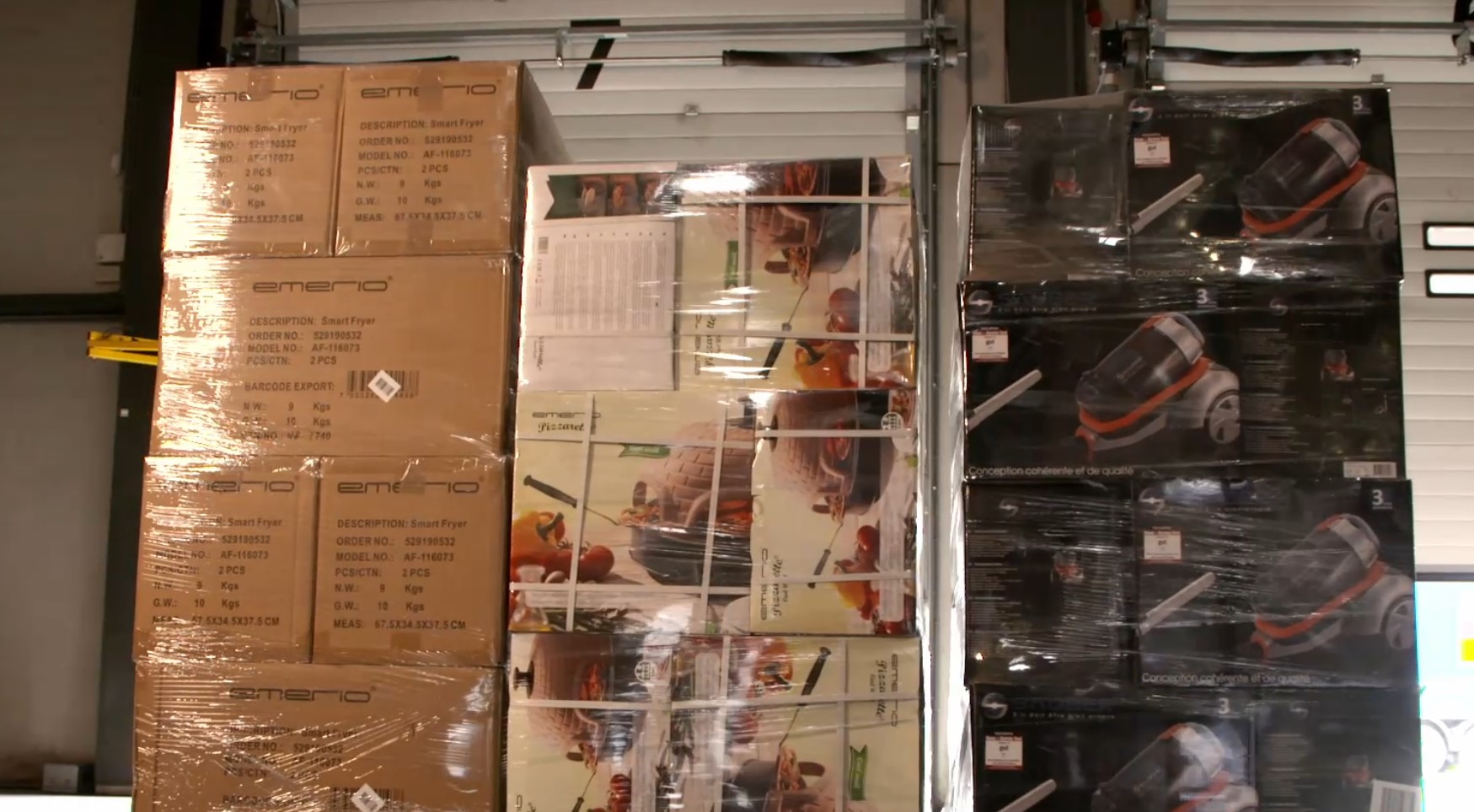
Incorporating teamwork
We have successfully combined our expertise in electrical household appliances with several well known laboratories on safety and testing. This is how keep track on new EU regulations. Together we offer you the most extensive and profound quality control to guarantee the success of our products.
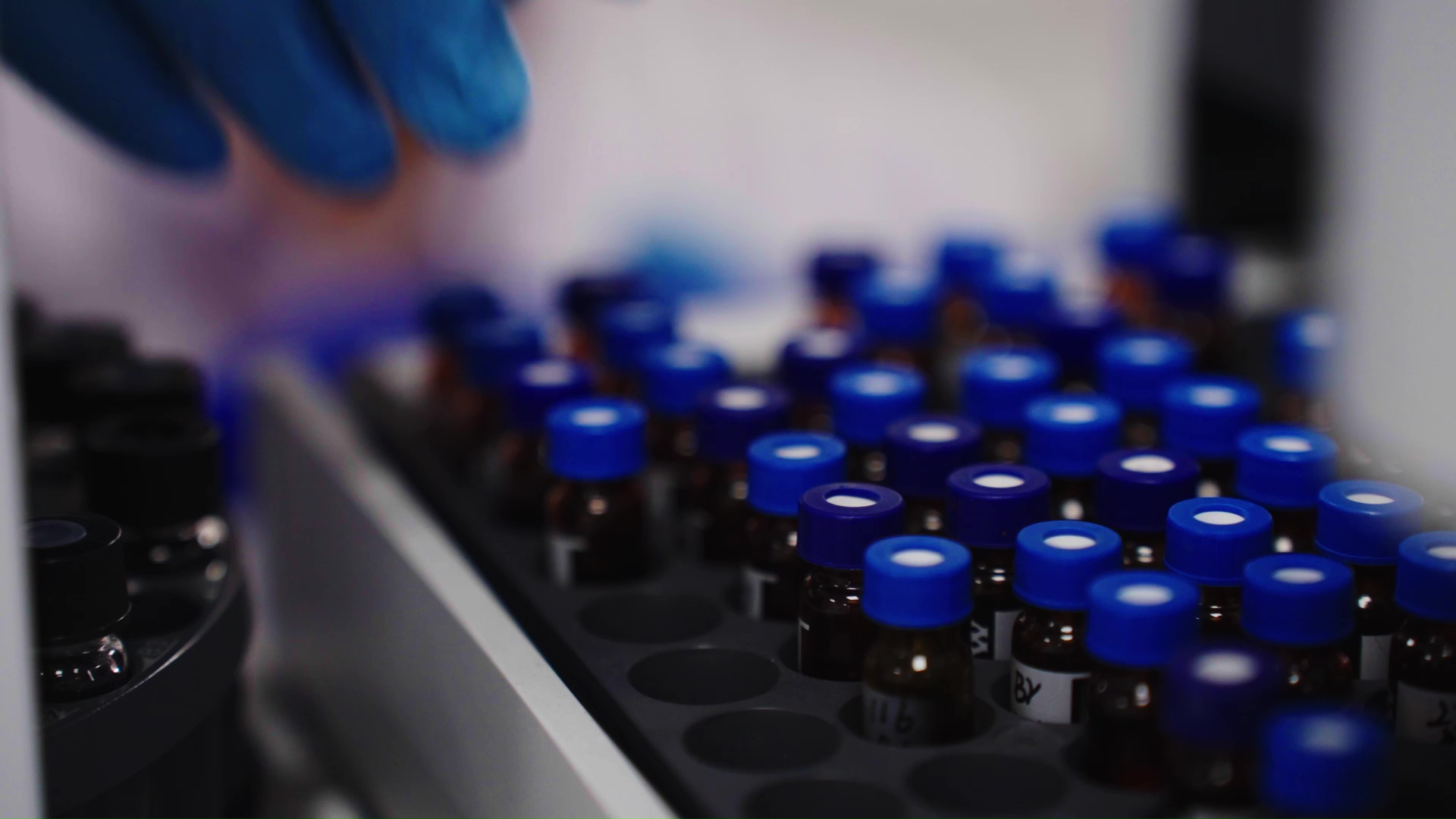
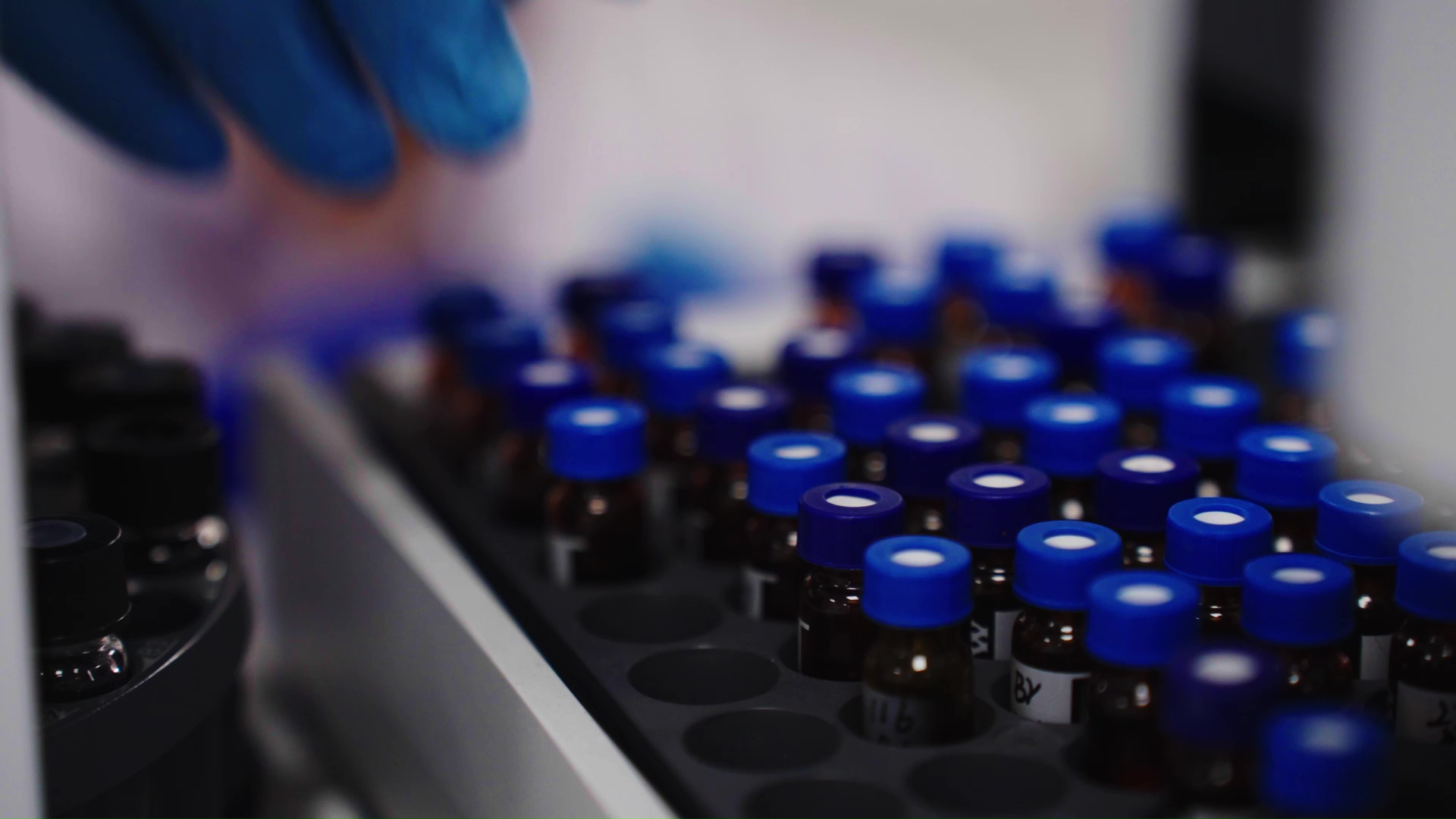
Our Approach
At Emerio we test all of our products extensively at every stage of the production process and we start even before we place an order. Our testing roadmap;
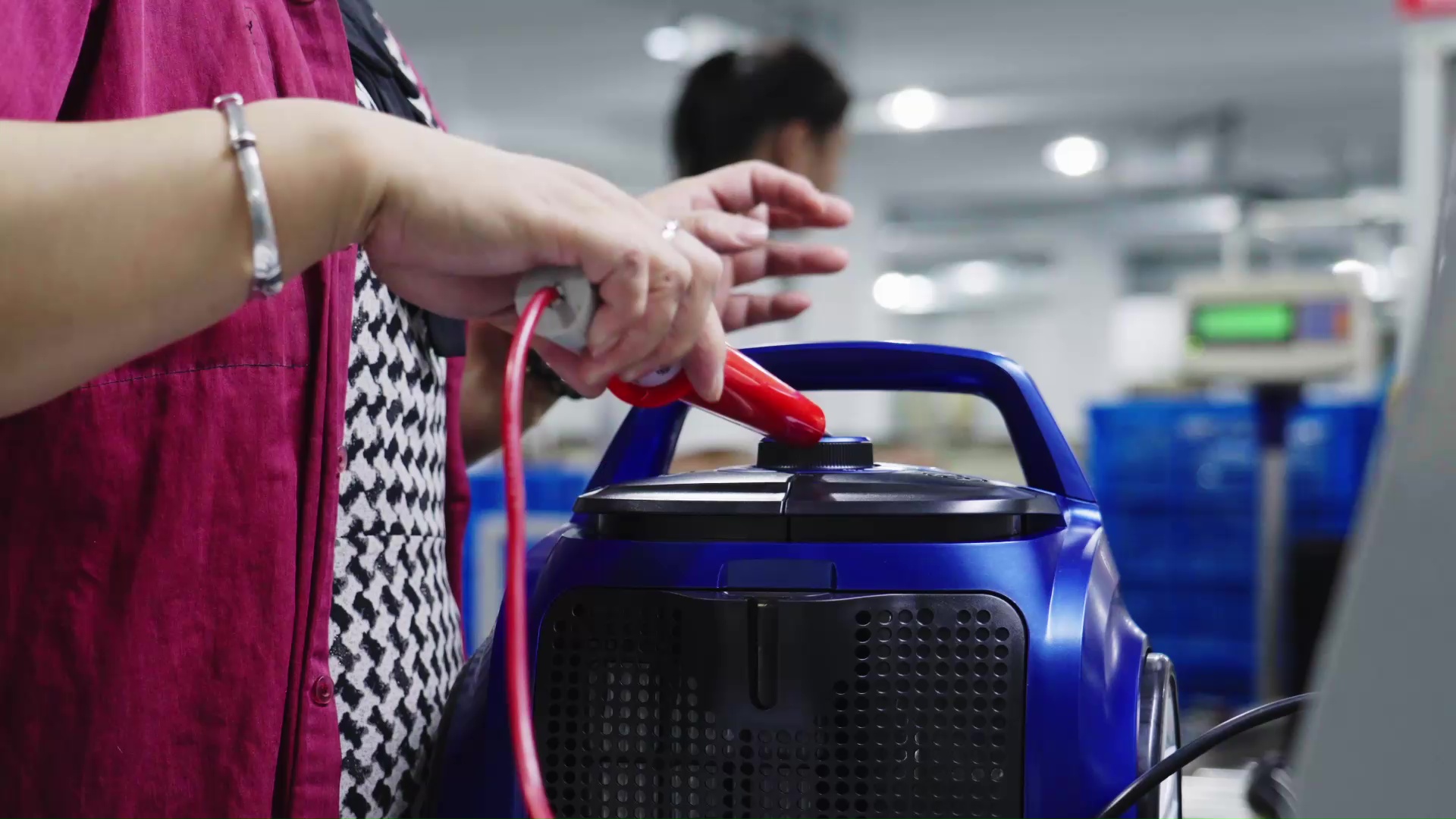
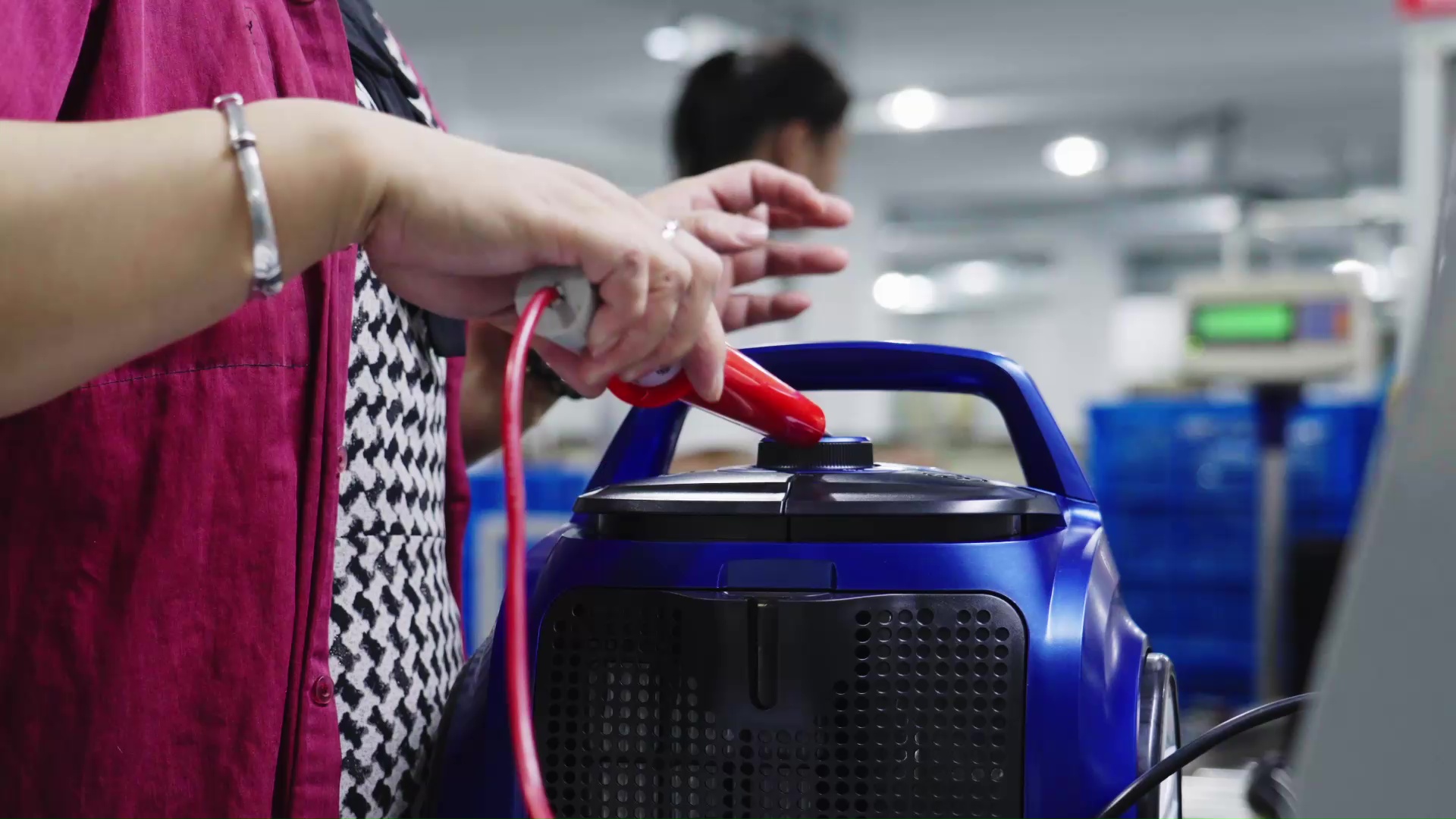
FACTORY AUDIT
Before Placing the Order
FACTORY AUDIT
Before placing an order we make sure that the producing factory has the necessary infrastructure, systems, processes and capabilities to execute it.
Our factory audit contains:
- manufacturing capabilities
- product risk analysis
- quality assurance
- material control system
- cleanliness, health and safety
- environmental compliance
- hazardous chemical management
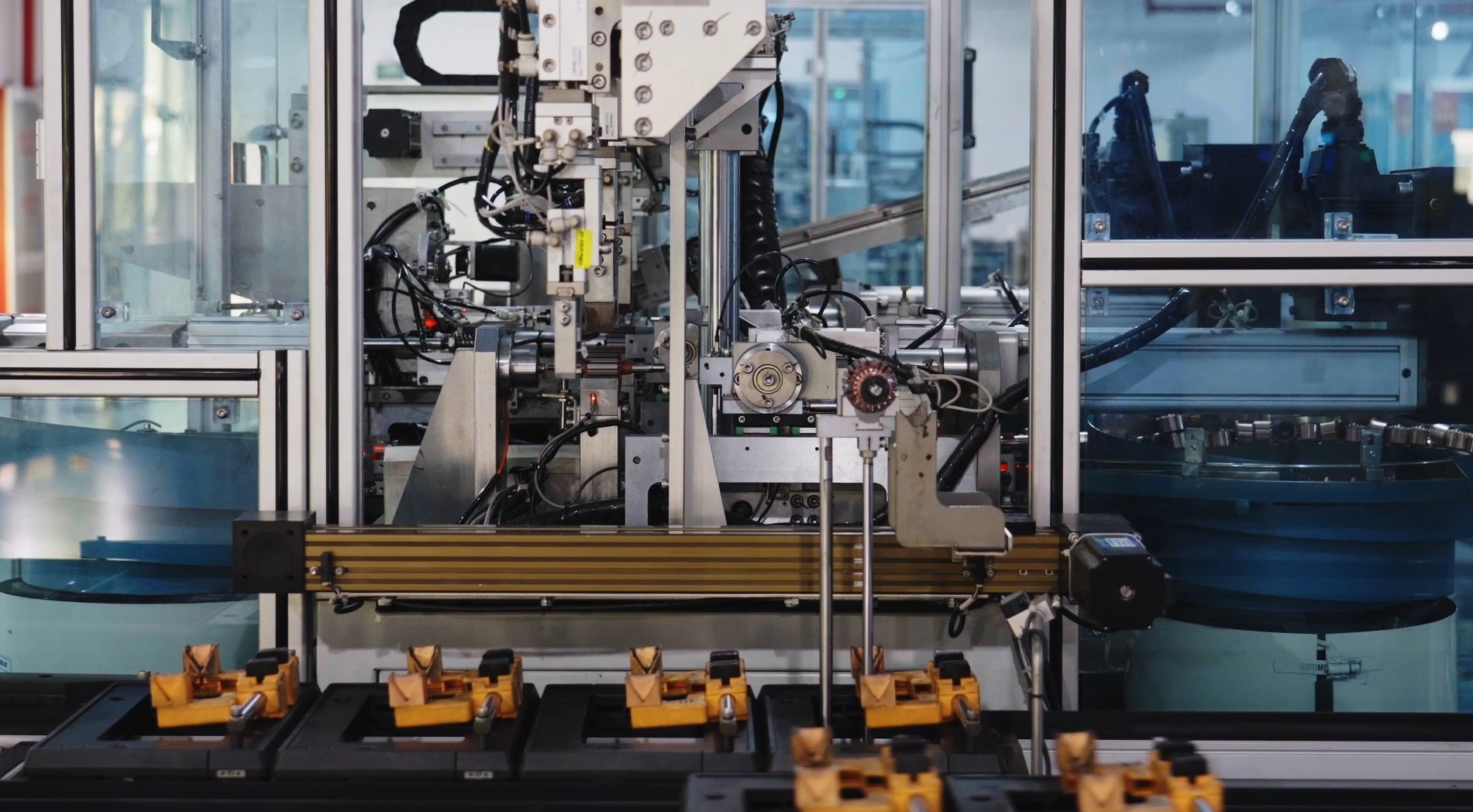
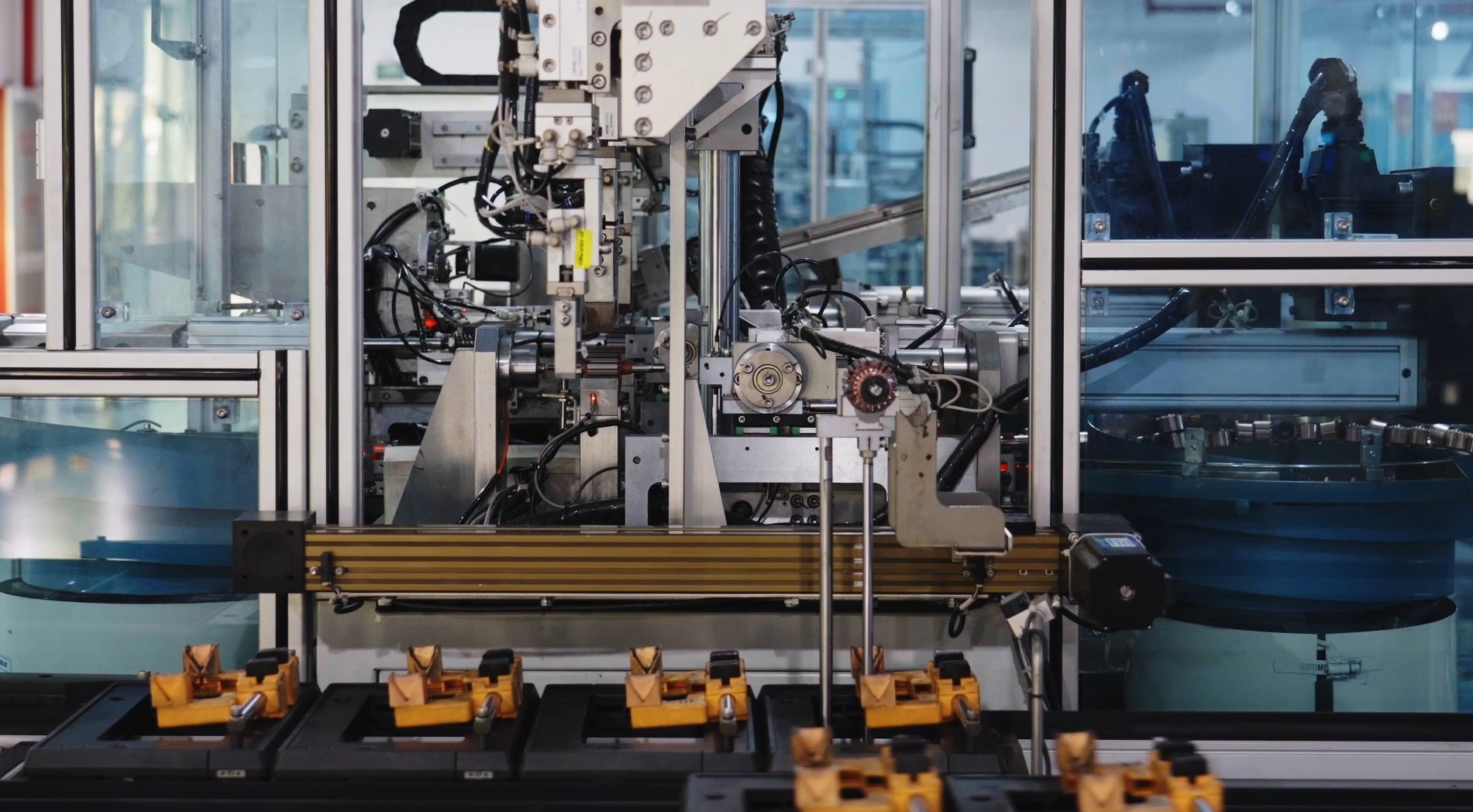
BSCI COMPLIANCE
Before Placing the Order
BSCI COMPLIANCE
We are a BSCI partner and ensure that our suppliers also comply with international standards, respect workers‘ rights and improve working conditions in the factories.
CERTIFICATION
We make sure that all certificates are correct and valid. We document all certificates accurately in our software database in Europe. Certifications prove your credibility in the market, but are only relevant if the products are produced accordingly.
QUALITY CONTROL DATABASE
We use our own software – developed and refined by our own experience over many years –to store and monitor technical documents and QC reports. All our offices have immediate access to important technical documentation.
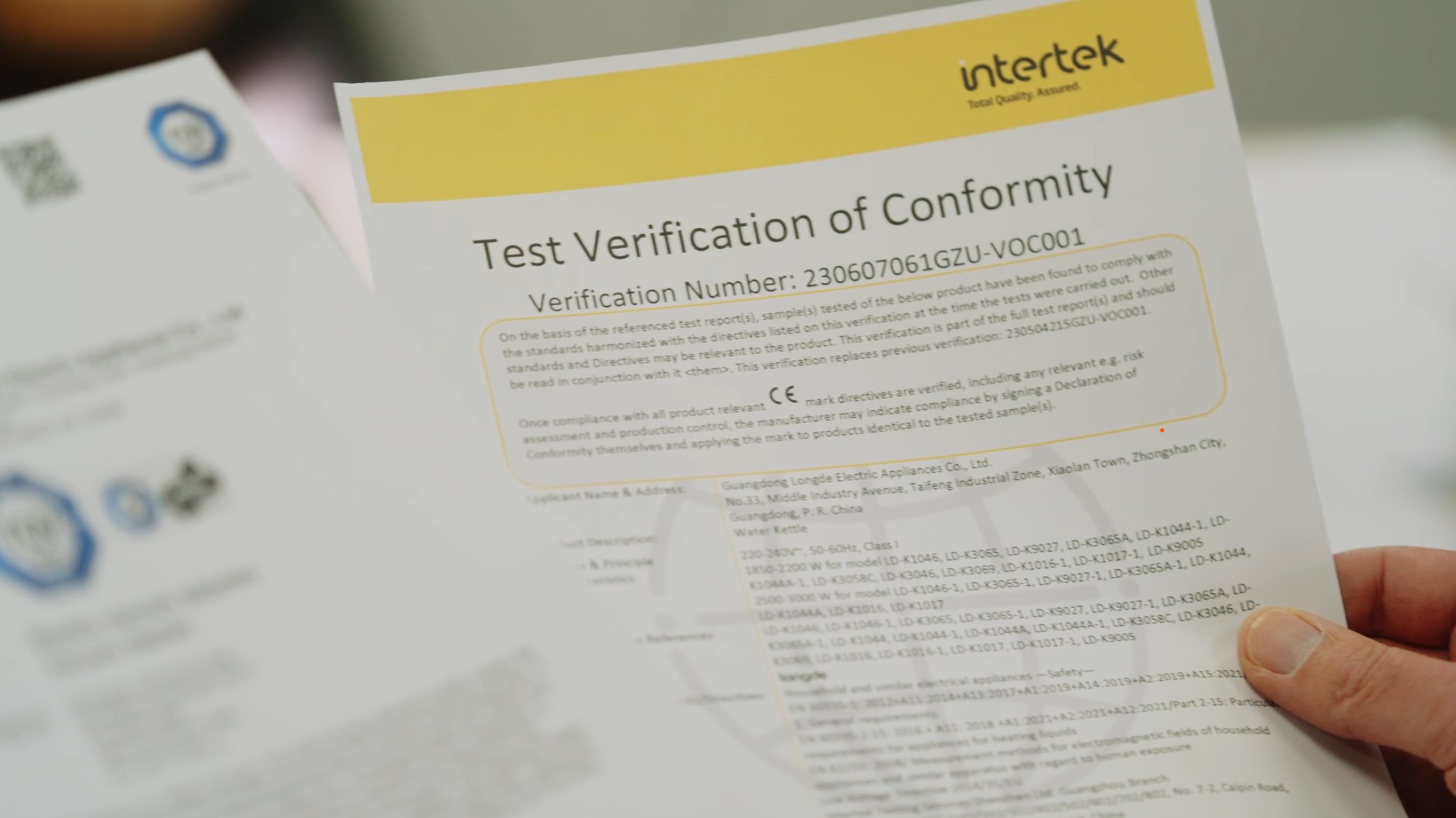
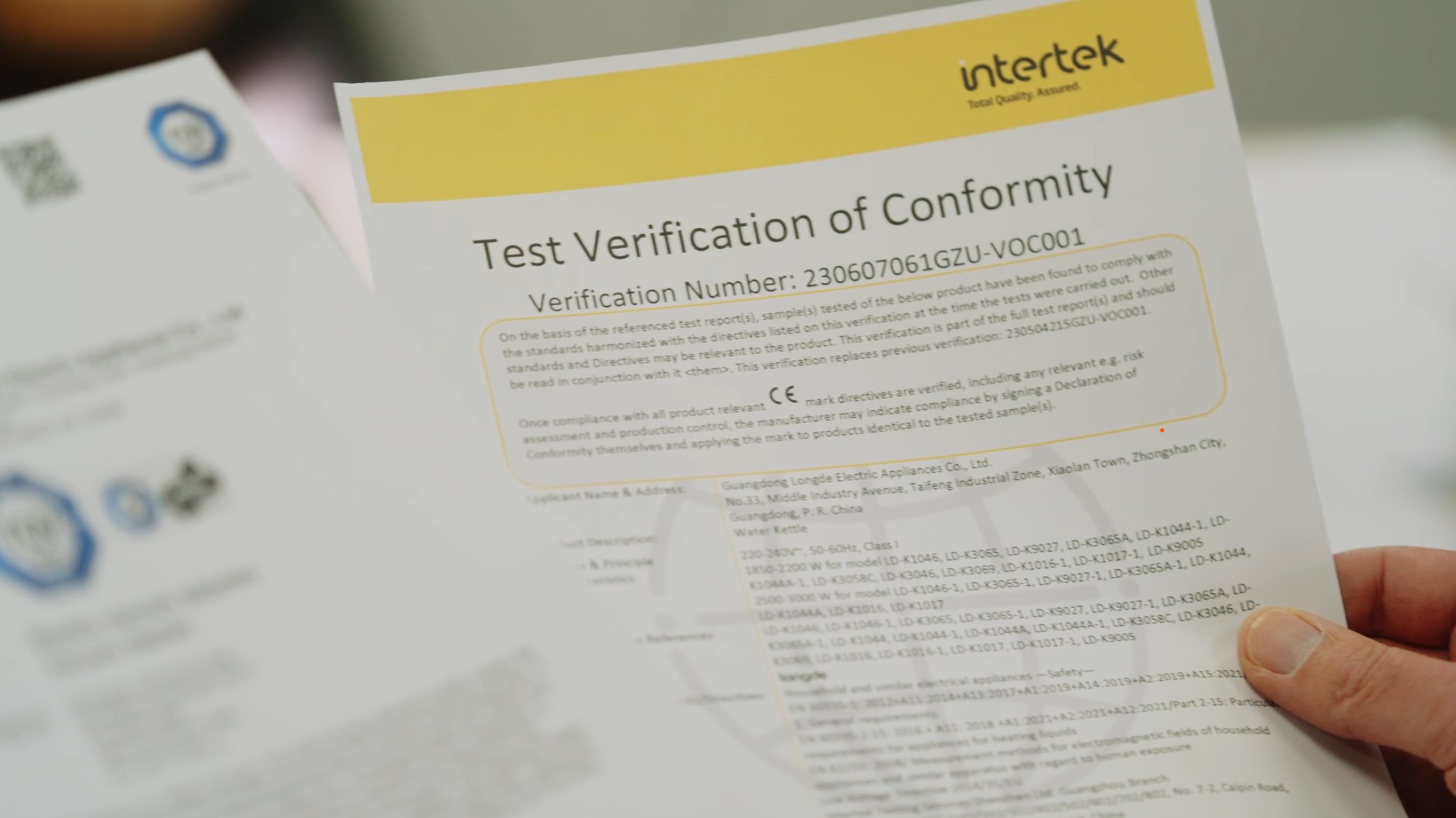
CONSTRUCTION CHECK
Before production
CONSTRUCTION CHECK
Our construction check contains:
- accessibility of live parts
- basic functional usage
- components
- creepage distances
- grounding
- hipot test
- instruction manual
- internal wiring
- rating label
- terminal connections
- sharp edges
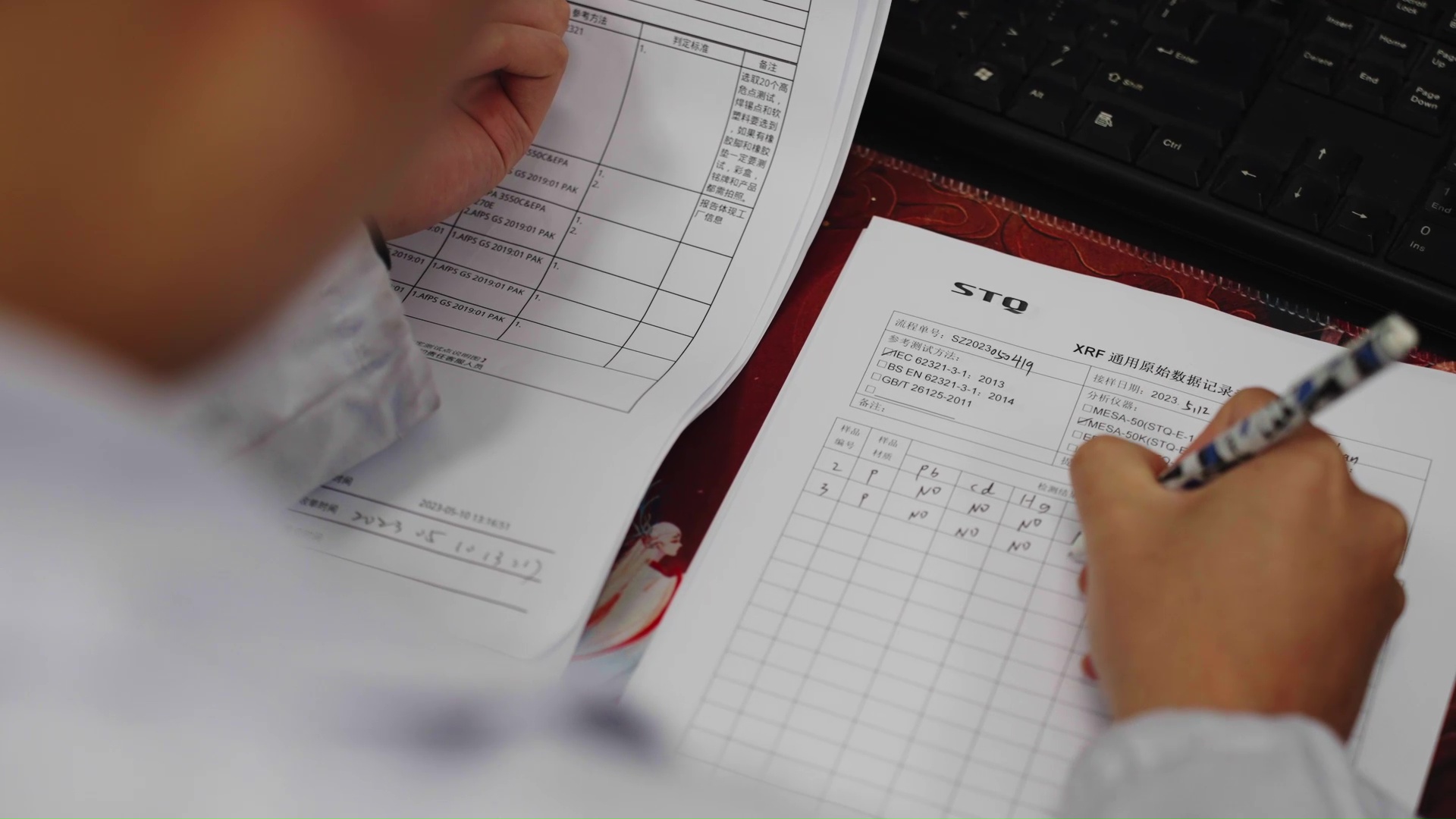
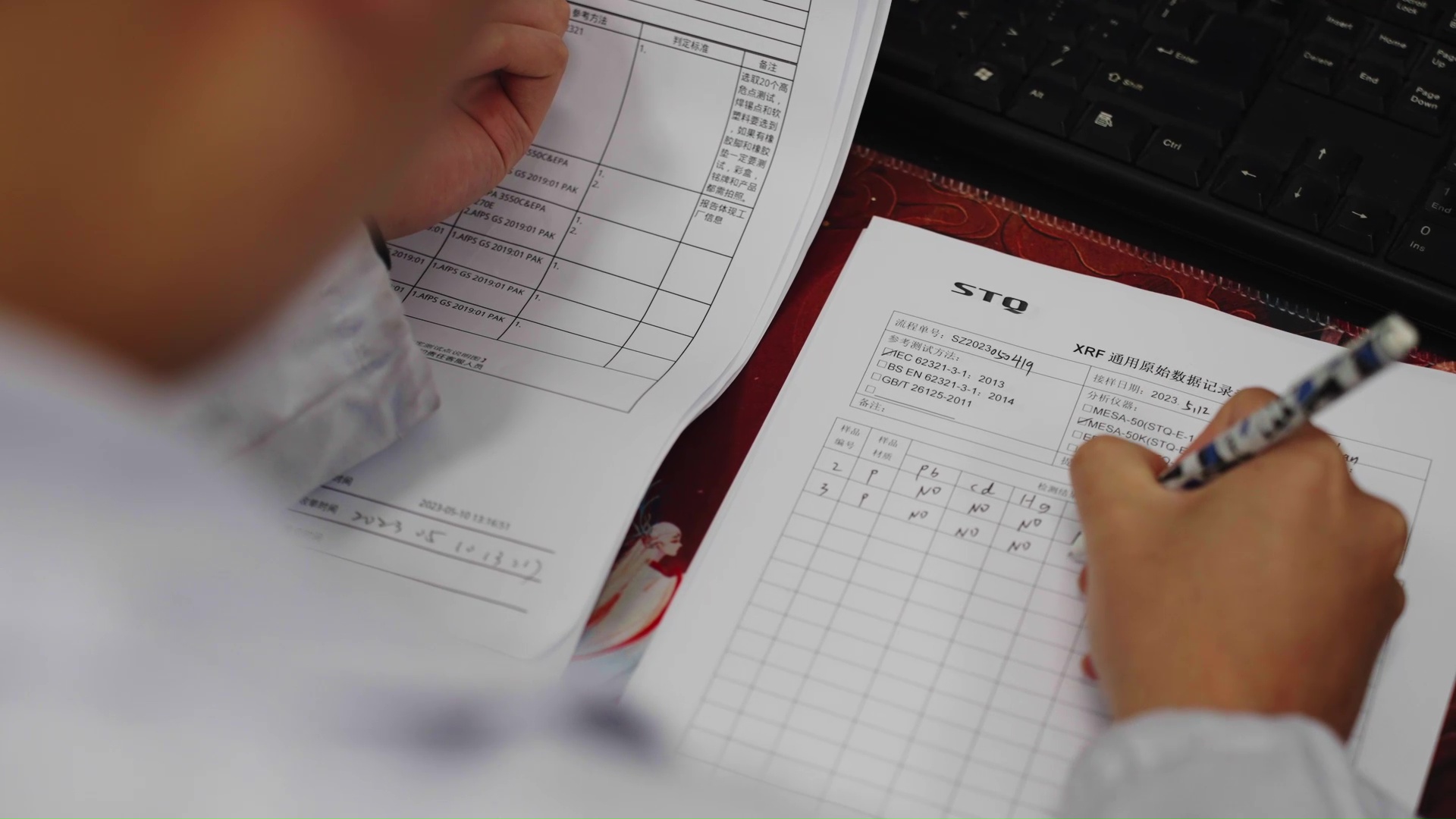
ABNORMAL USAGE TEST
Before production
ABNORMAL USAGE TEST
We test any kind of potential abnormal use of the product by the consumer.
This check is based on:
- product history
- product group
- Rapex history
- QC management
- Test laboratories experiences
Examples:
- What will happen if the consumer fills the kettle with too much water?
- What will happen if you reduce the speed and airflow on a fan heater?
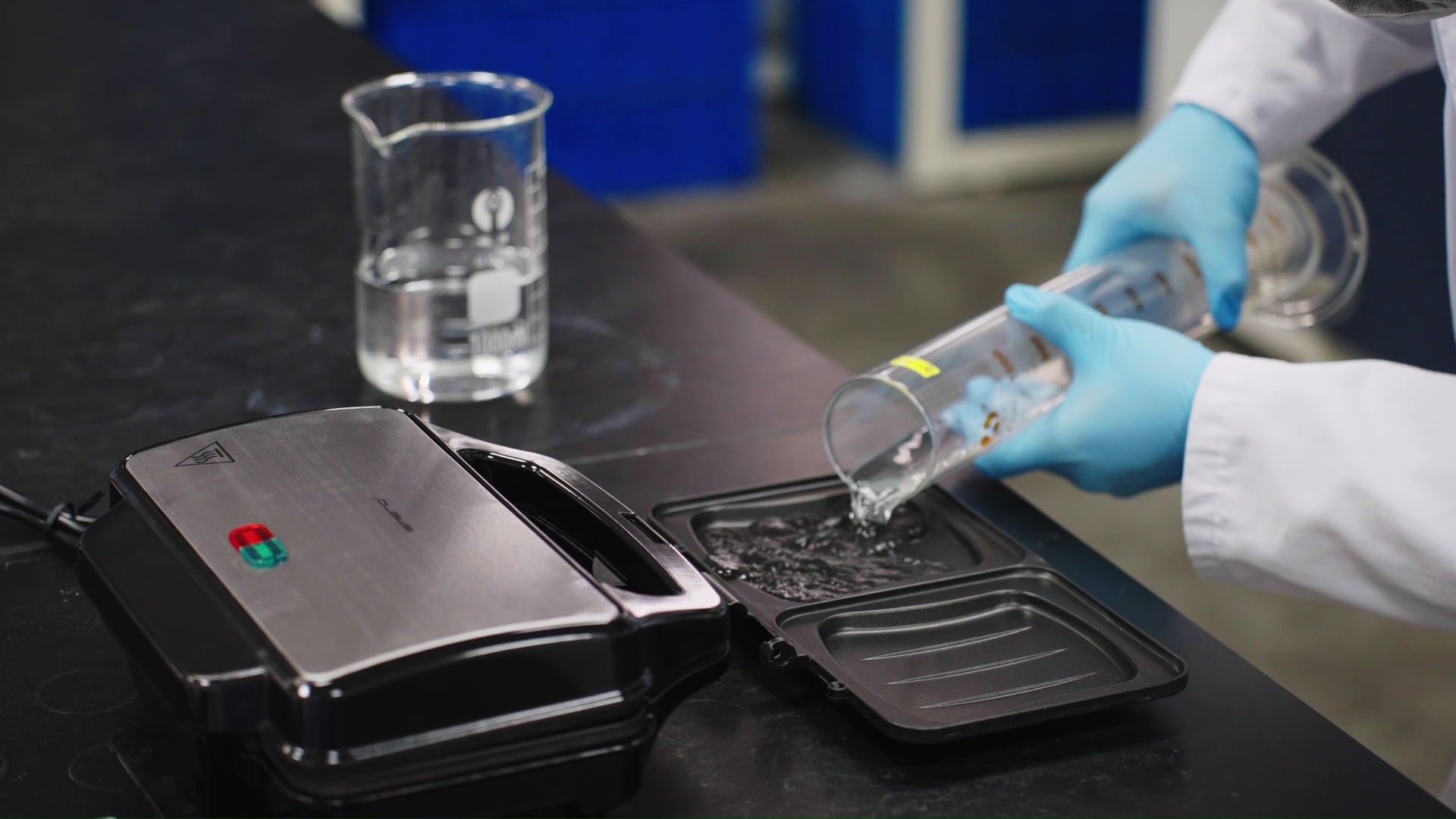
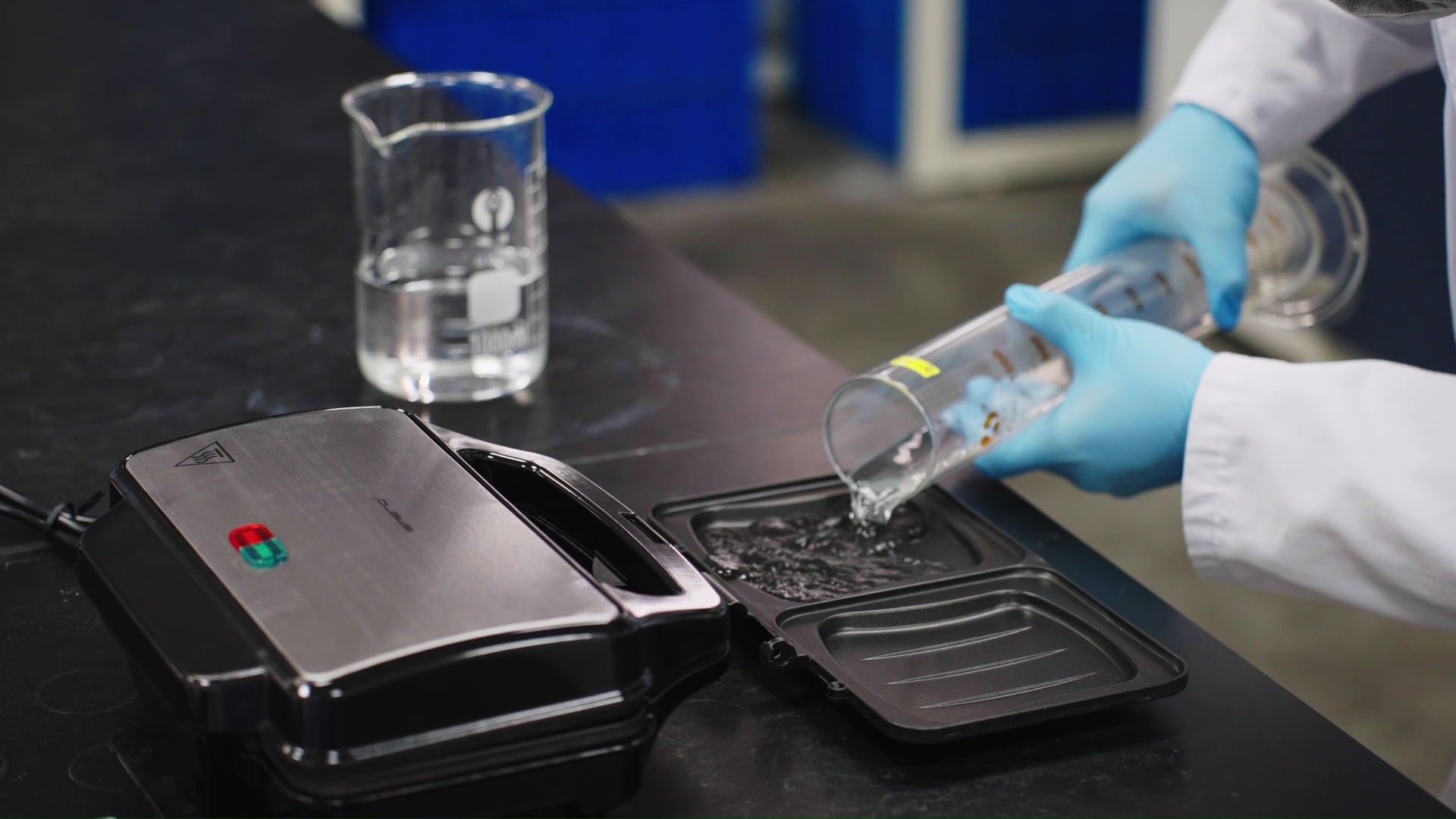
QC PLAN
Before production
QC PLAN
Our QC managers accurately plan what additional tests are necessary for each individual order. This plan is coordinated with our merchandisers, who monitor the orders until delivery.
Our QC managers' decisions are based on:
- product history
- product group
- Rapex history
- QC management
- Test laboratories experience
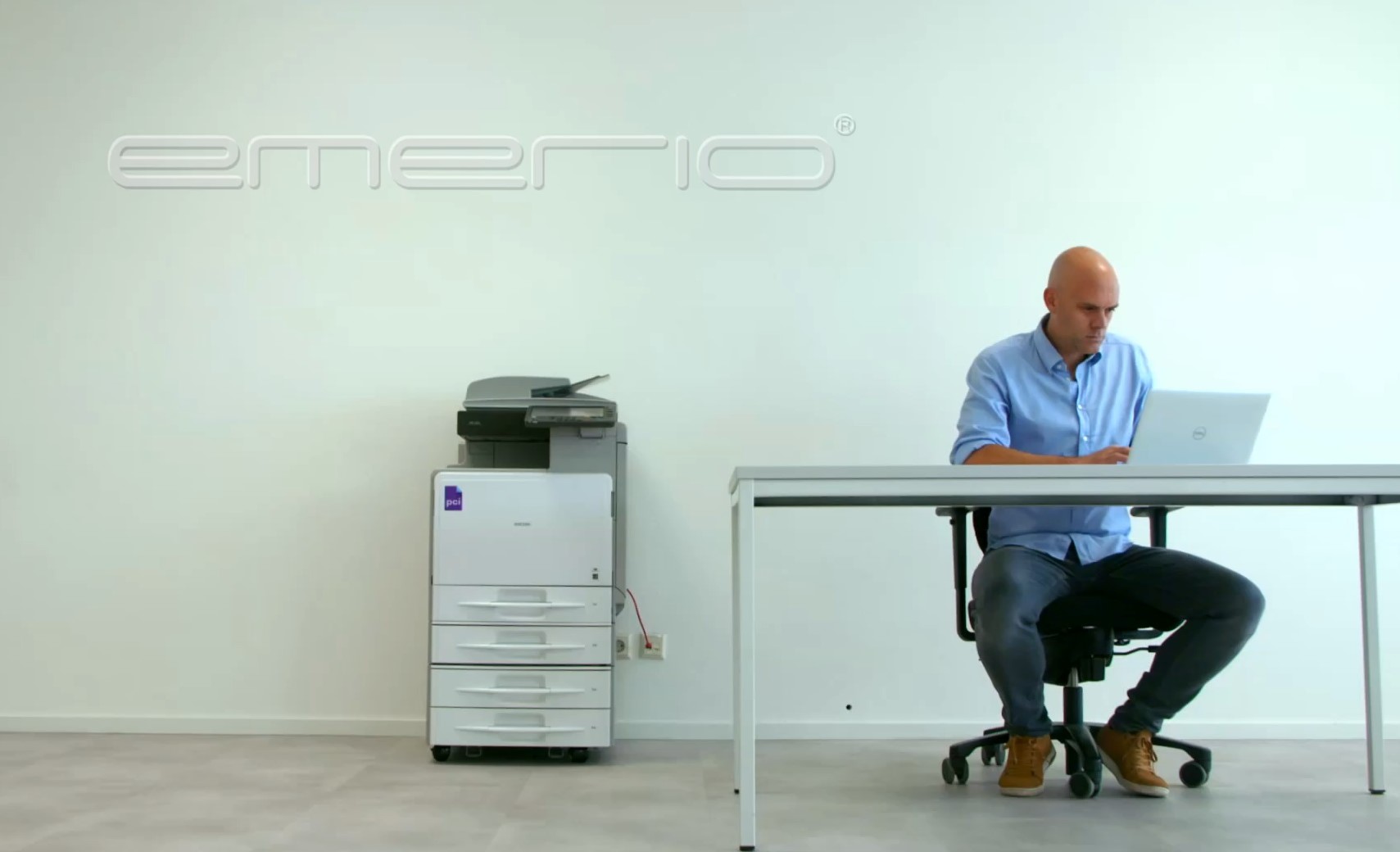
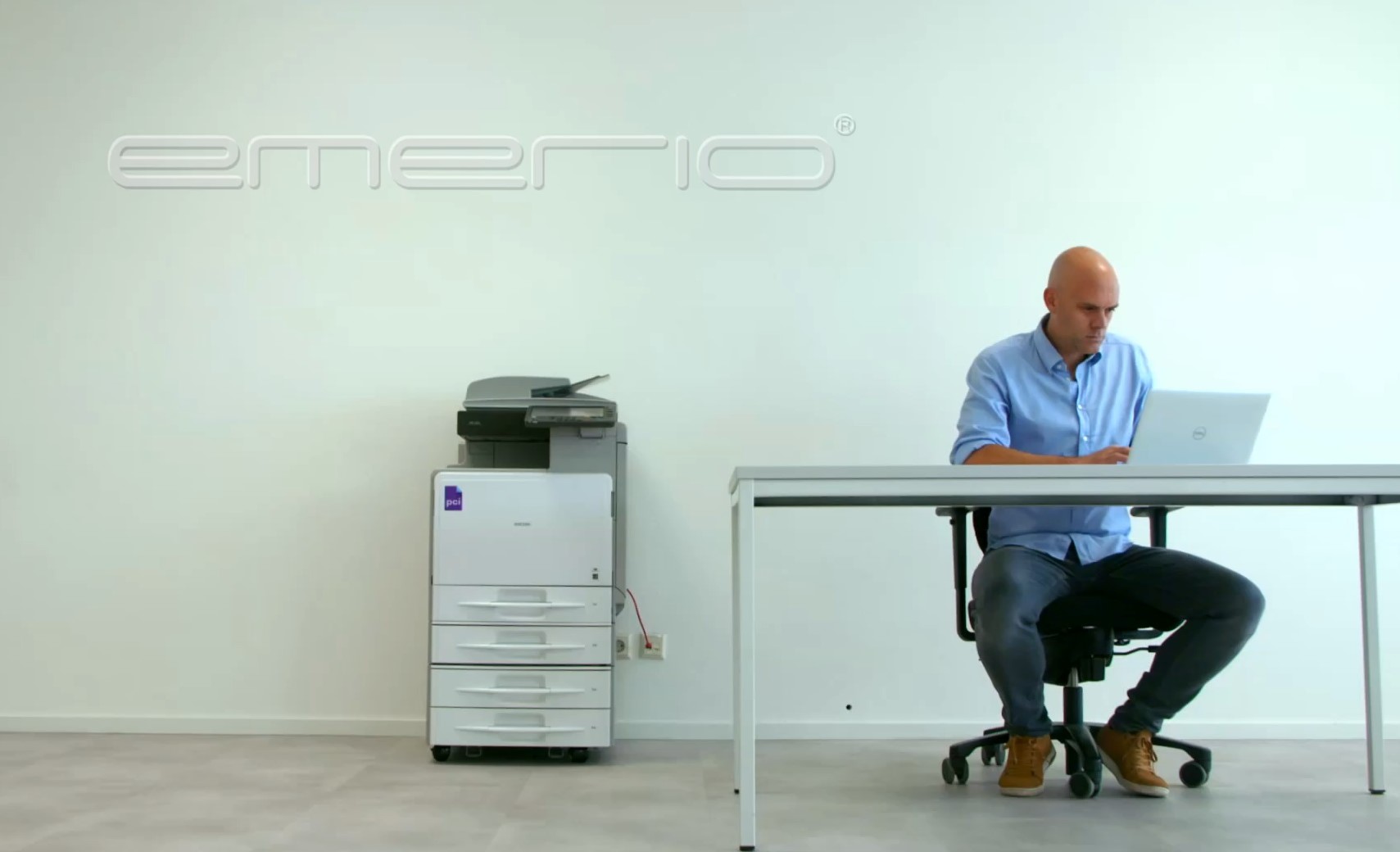
OUR QUALITY CONTROL DATABASE
Before production
OUR QUALITY CONTROL DATABASE
Movies and pictures can be added to our database to help our QC staff prove problems.
To avoid problems occurring repeatedly, we store the history of complaints about a particular item or product group in our database.
We scan each Rapex report for household appliances weekly. We analyse them together with test laboratories to investigate the recalls of similar products from other producers. Thus, we ensure that these mistakes will not happen to our products.
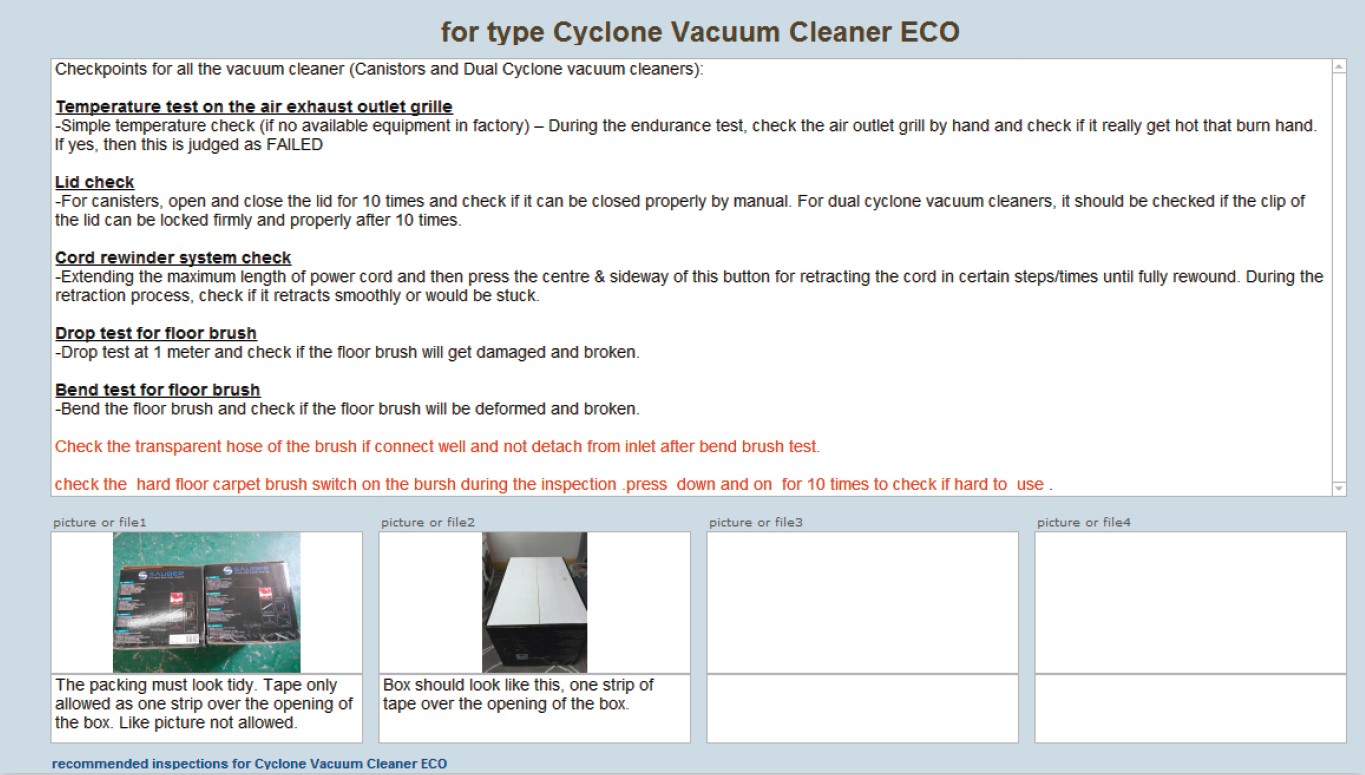
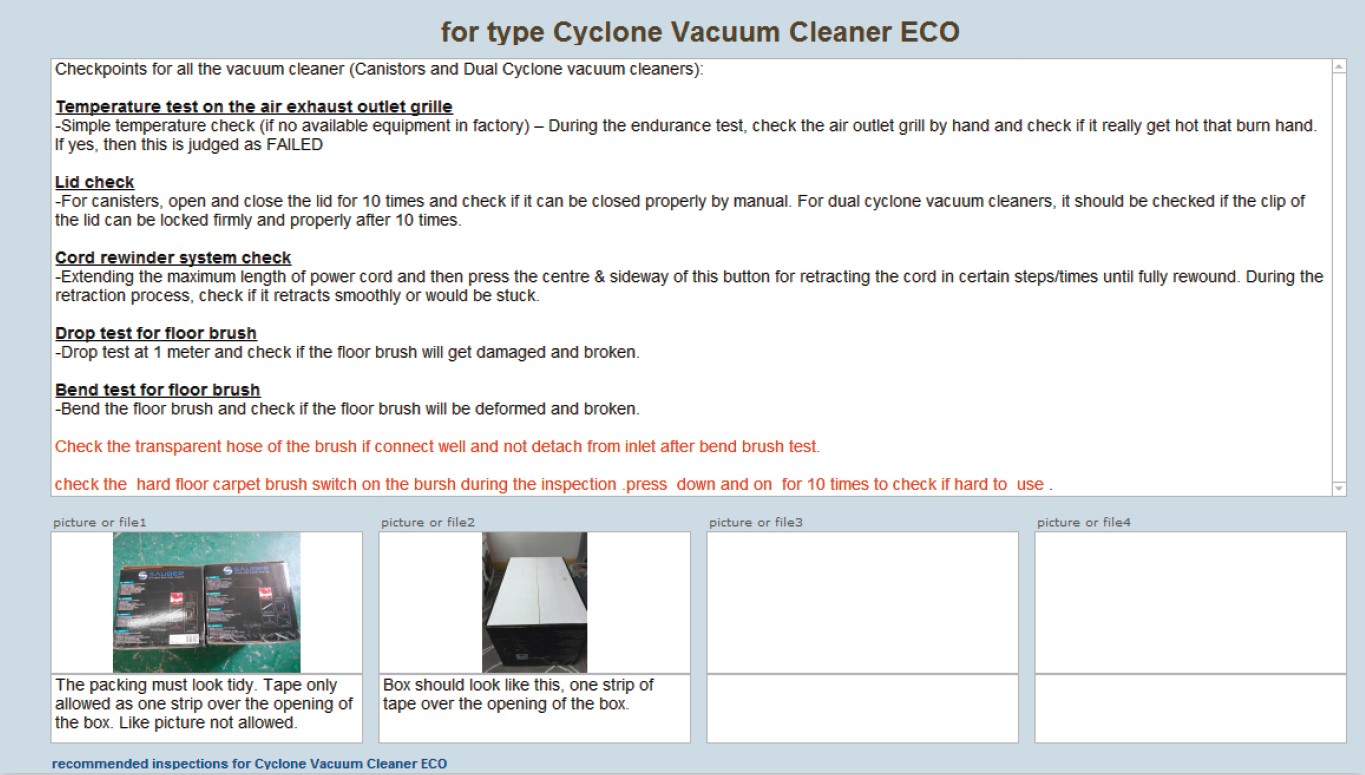
ONLINE INSPECTIONS
During production
ONLINE INSPECTIONS
We carry out online inspections when 10–15% of the production is completed. We inspect the production batch and examine the products in the line for possible defects. At this point we identify deviations and offer advice that will ensure the uniformity and the quality of the product. We also recheck for any defects discovered during preproduction inspection and confirm that they
have been rectified.
We survey a minimum of twenty samples or more if available. The tests are performed according to ISO 2859-1, Level 2 and Level 3. We use our database
to recognize previous problems and to focus on knowledge we have gained from the past.
The inspection also includes:
- abnormal usage test
- additional tests
- designated component control
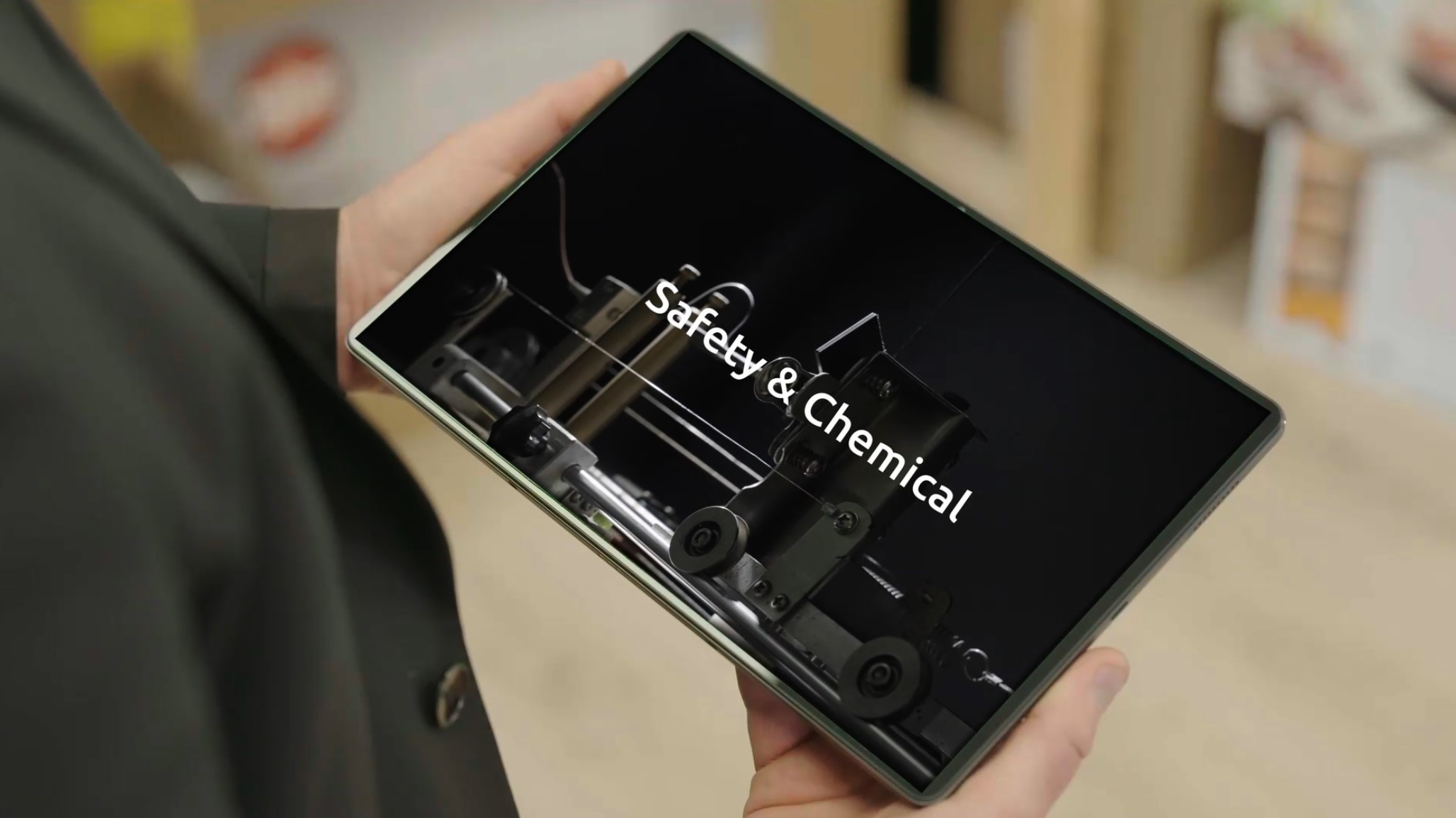
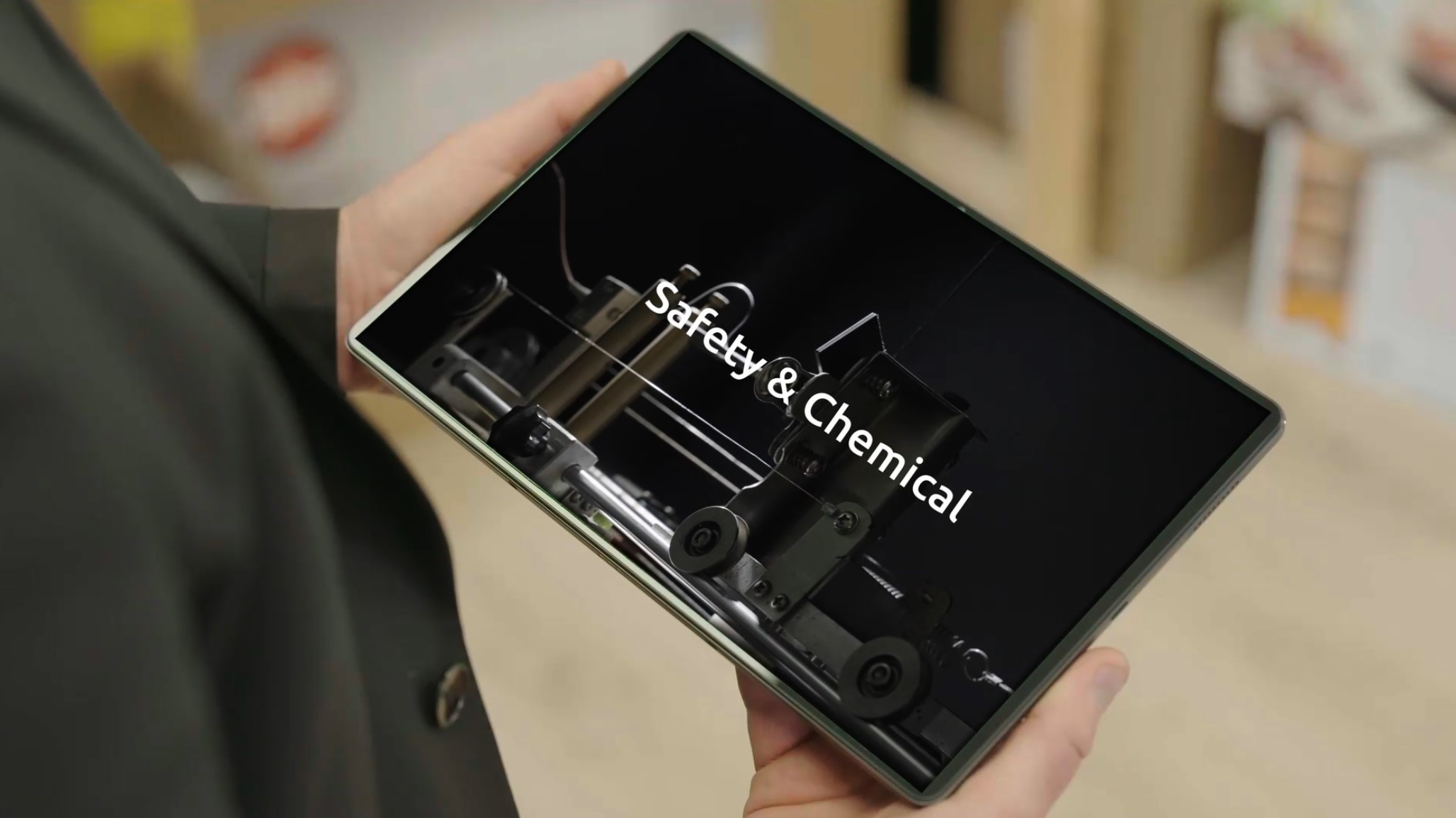
FINAL RANDOM INSPECTIONS
After production
FINAL RANDOM INSPECTIONS
These inspections are to begin after production has been completed and all merchandise is ready and packed for shipment. Our FRI inspection is
performed according to FRI standard Level 2 and 3 to verify product safety, quantity, workmanship, function, colour, size, packaging, and more.
Together with the test laboratories we check the QC history in our own database to ensure previous problems no longer occur.
Our FRI inspection is performed according to ISO 2859-1, Level 2 and Level 3:
- abnormal usage test
- additional tests
- designated component control
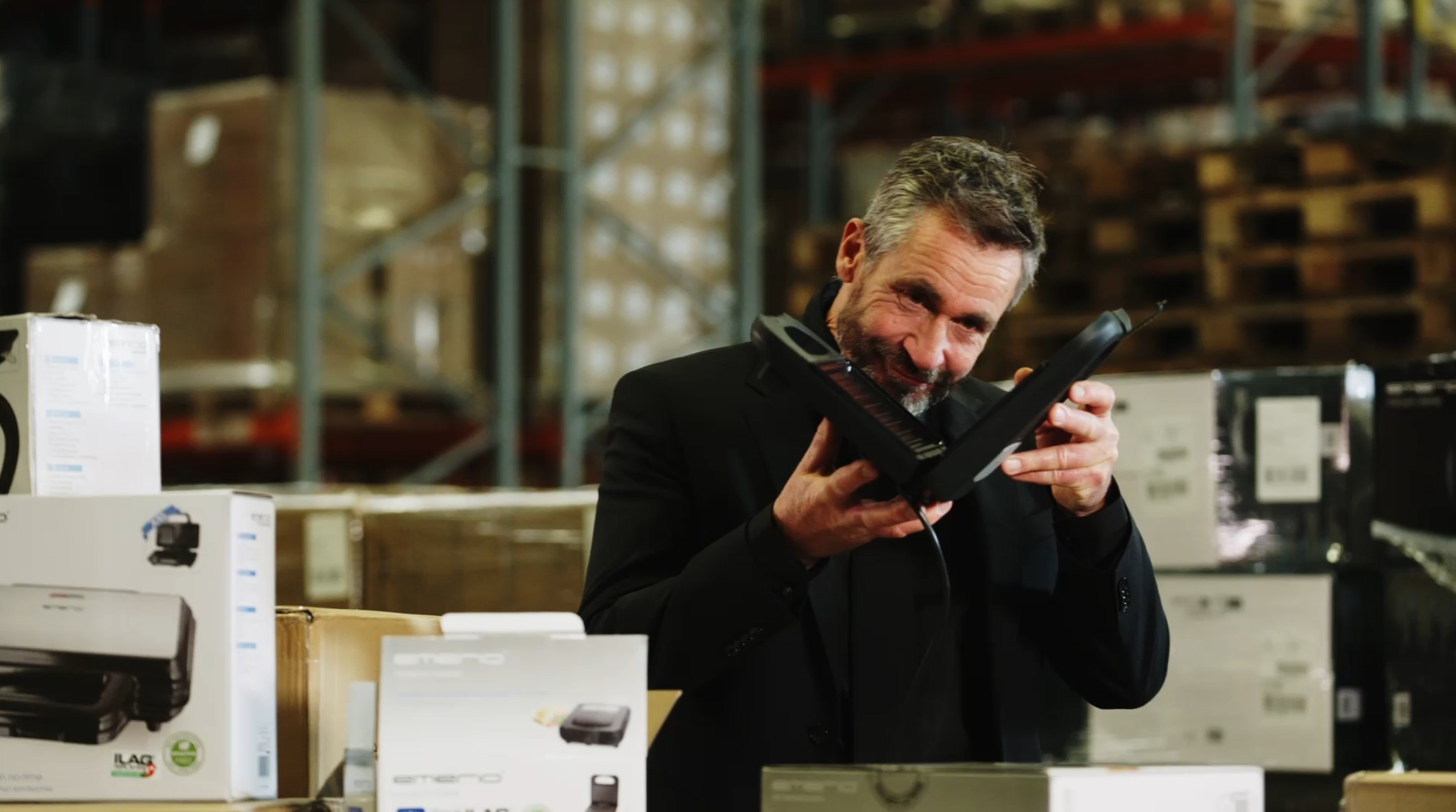
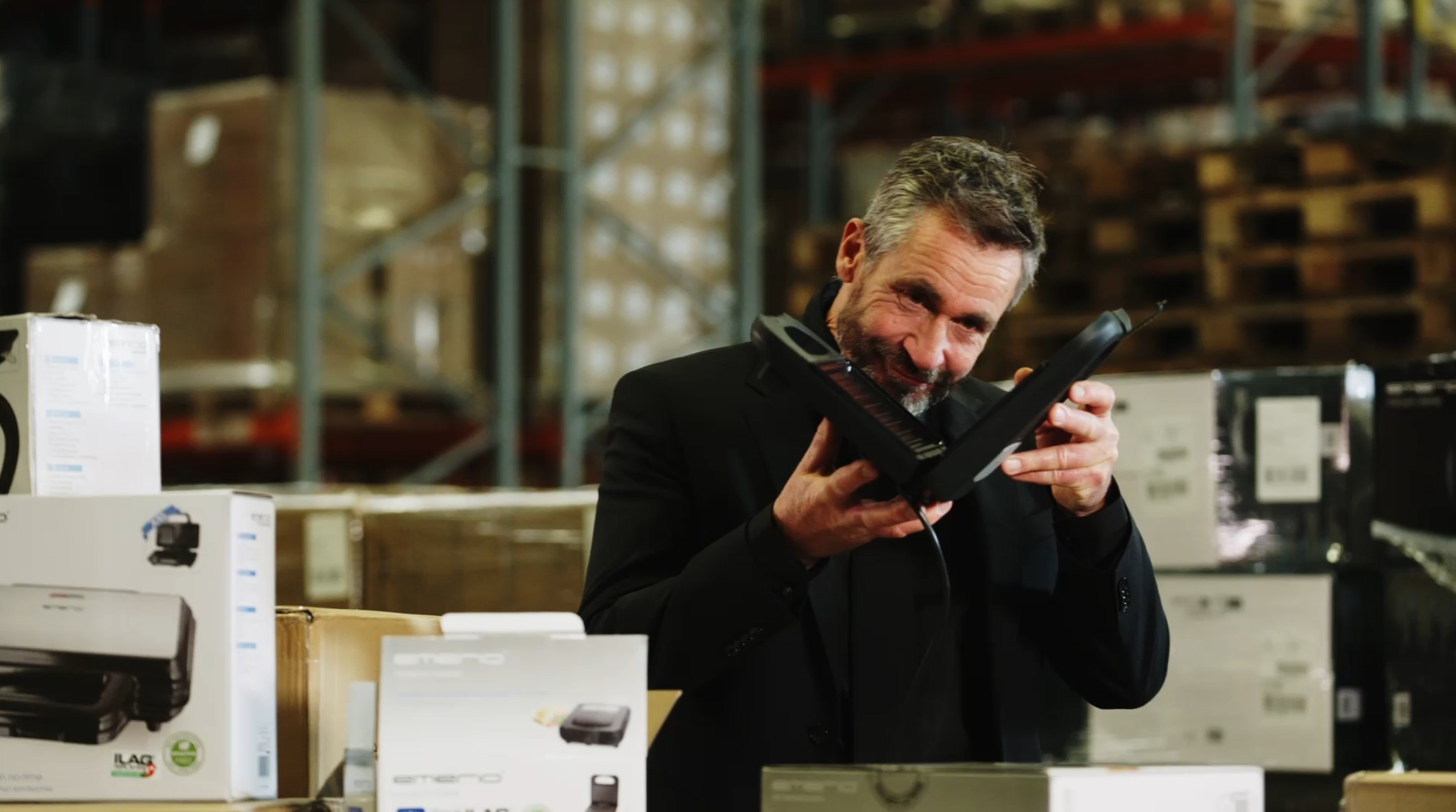
INSPECTION OF RETURNS
After sales
INSPECTION OF RETURNS
Our rating labels state a number for each order that enables us to pinpoint the production date, inspection date and inspection reports. This way we are able to integrate the knowledge acquired from the defects into our quality control cycle to improve future products.
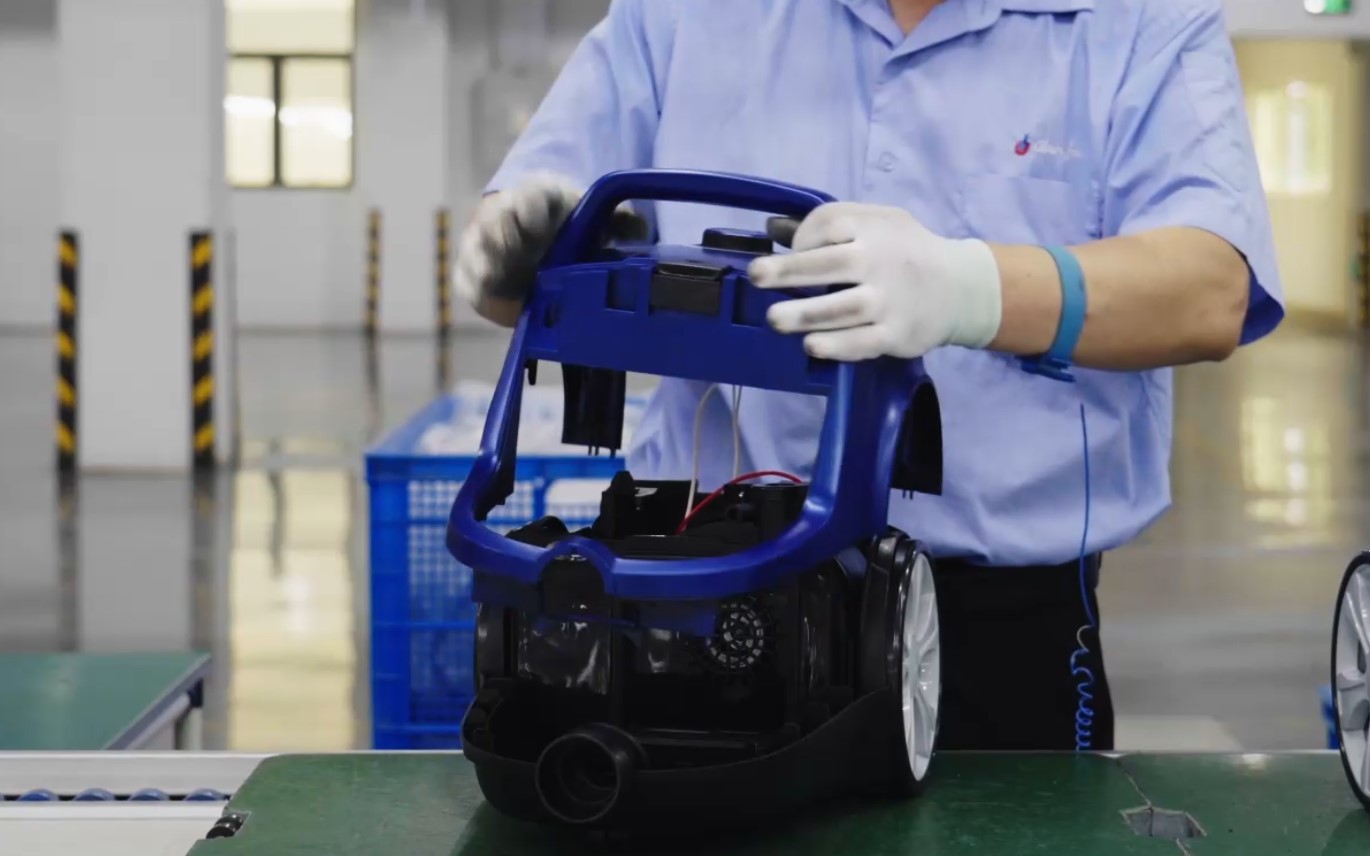
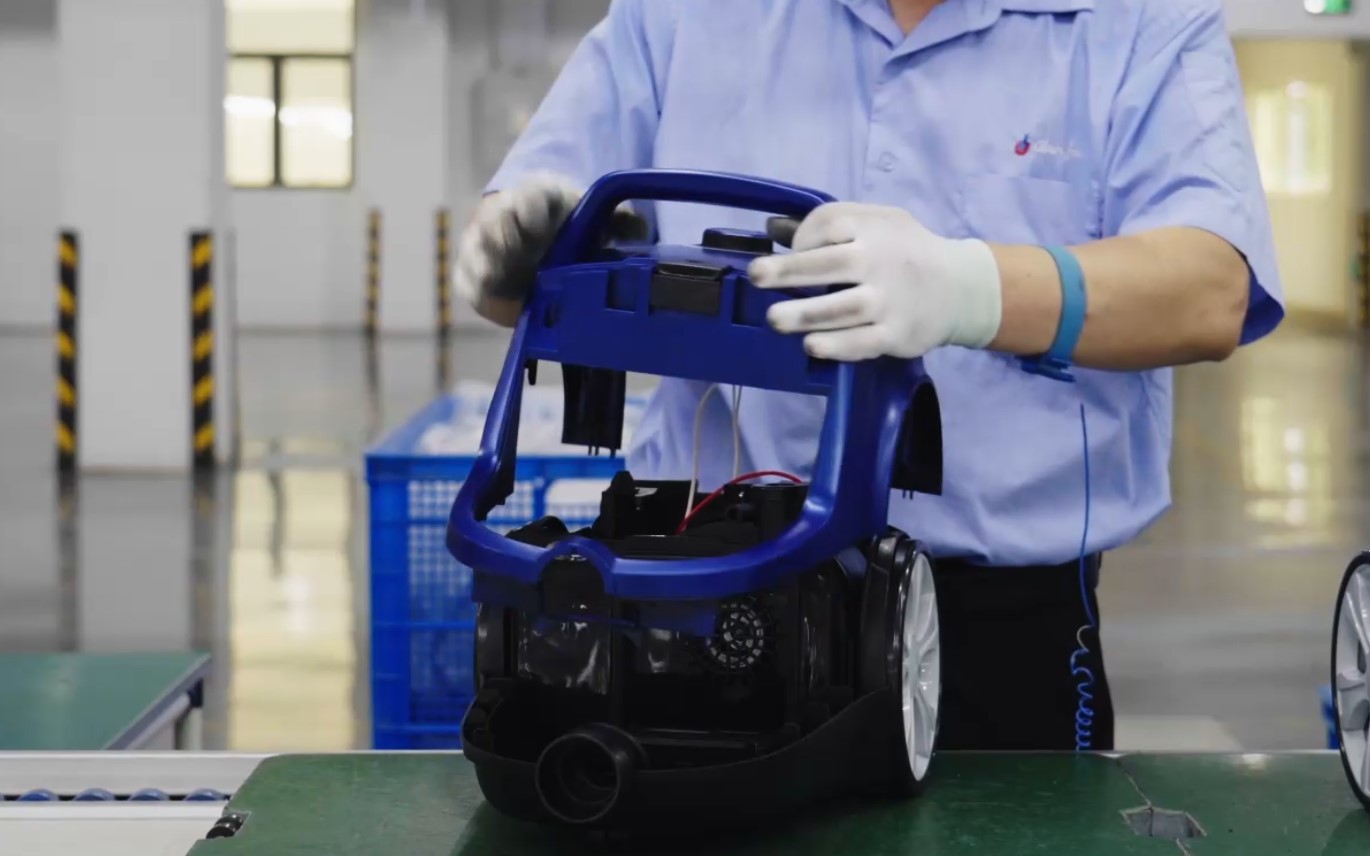